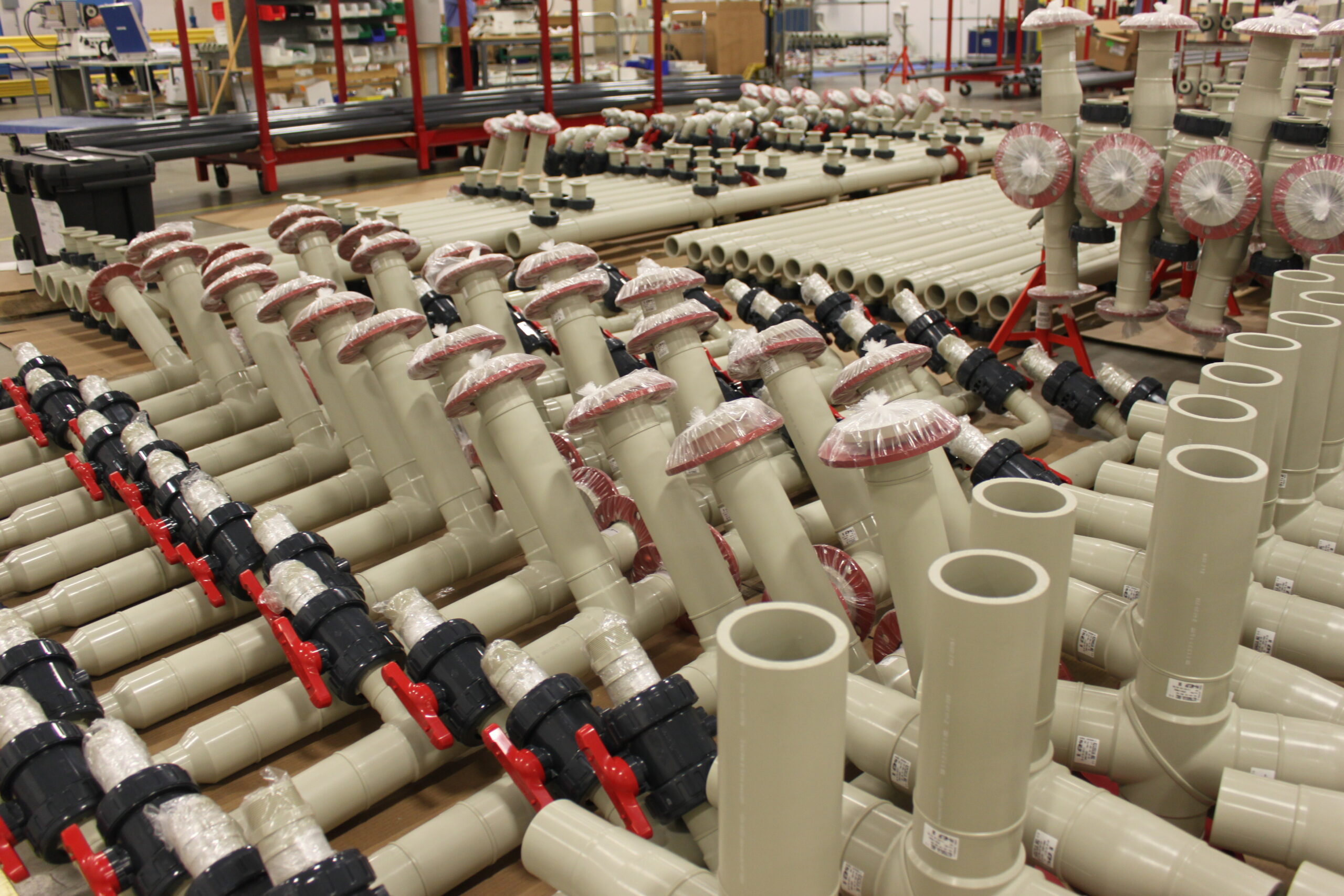
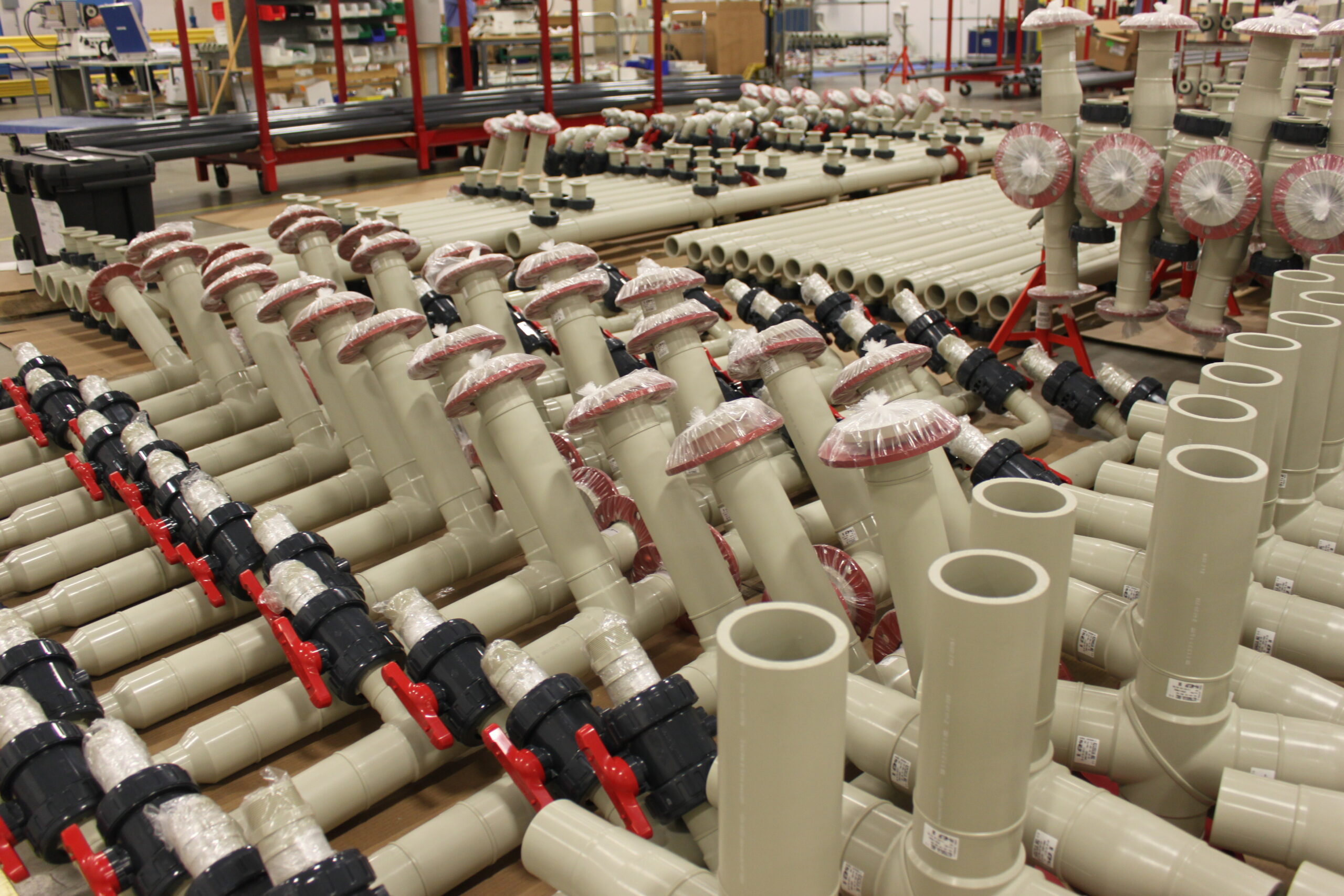
May 1, 2024
Inner Circle
Why Expertise Matters in Fabrication
Contributed by Brian Zagrodny, National Fabrication Sales Manager
Significant industrial growth in the last decade has challenged industries and contracting firms to construct and deliver completed facilities as contracted quickly. The goal is to complete the build in record time and under budget and not compromise quality. Today, job sites are congested and cluttered with competing trades, and everyone strives to deliver their scope of work as committedly as possible. Offsite manufacturing (OSM) is becoming widely leveraged as the answer to meeting these challenges.

Technologies and tools like Building Information Modeling (BIM) and Computer-Aided Design (CAD) have proven essential in the planning and layout of piping systems in prefabrication. These technologies allow for pre-production review of the design methodology, detection of potential clashes, and decrease in waste, to name a few. By addressing areas of concern early on with the designers, integrators, and fabricators, corrective action can be taken to reduce the risk of time delays, design flaws, and unnecessary materials and components being utilized.
Offsite manufacturing facilities with a well-established fabrication infrastructure are positioned to deliver high-quality results that might not be realized in certain instances with stick-built construction. There, dedicated specialty fabricators work in a climate-controlled environment, fabricating to strict build specifications and tolerances where piping material, welders, and tooling are all in the same tempered indoor facility—creating work cells and stations where high-quality and often highly repeatable work can be performed with consistency and accuracy. Throughout the process, quality control workers inspect finished and unfinished goods to ensure that specifications, tolerances, and other specific criteria are met to produce a better product.
However, OSM goes far beyond merging two or more components together. At Asahi/America, spools and assemblies undergo rigorous quality control procedures and dimensional verifications throughout our fabrication process. These steps help ensure that the fabricated spools meet the required quality and dimensional tolerances before they are shipped and installed on-site. This allows for better traceability of material and processes and can aid in resolving quality or dimensional issues.

With project demands increasing and base builds becoming more complex, the need for spool mapping and weld logging is growing. With these logs, project managers and installers can accurately identify where spool assemblies are installed and identify weld criteria for greater accountability. Spool mapping consists of referencing specific prefabricated sections and indicating the exact location and orientation on a drawing or pipe map. The weld log captures critical weld data like the welder, tooling, weld parameters, and when the weld was performed.
Other considerations in OSM include the need to have assemblies tested prior to shipping. At Asahi/America, we offer optional hydrostatic and pneumatic testing, where we monitor pressure over a specific duration to ensure there are no leaks or pressure drops.
Other factors when considering OSM include mitigating risk, safety, availability of skilled labor, recovery schedule, etc. While cost as a stand-alone is often hard to quantify in many instances, it does afford a couple of key benefits, one of which is cost certainty. Cost certainty is the assurance that the overall costs associated with a prefabricated deliverable(s) are accurately priced and that that price is upheld throughout the fabrication build regardless of issues/errors and wasted material on the fabricator’s behalf to produce the deliverable (assuming no changes or variations are made to the scope of work). Another factor to consider, which compliments cost, is schedule certainty. Schedule certainty is essentially the assurance of delivering on schedule and is a key contributor to a project recovery schedule.
In closing, offsite manufacturing has gained approval and is being increasingly leveraged throughout the construction industry because of the value it delivers. Some of the most significant considerations driving OSM have been cost savings, improved quality, and faster close-out turnovers. However, the benefits are rapidly expanding to include safety, a shortage of skilled labor, and overcoming logistical challenges.
If you would like to learn more about Asahi/America or if prefabrication may be right for your project, don’t hesitate to get in touch with Brian Zagrodny.
EDITOR’S NOTICE: Please note, the information in this article is for educational purposes only and does not supersede any Asahi/America technical information or product specifications. Please consult Asahi/America’s technical department at 1-800-343-3618 or pipe@asahi-america.com on all product applications in regards to material selection based on the pressure, temperature, environmental factors, chemical, media, application, and more.