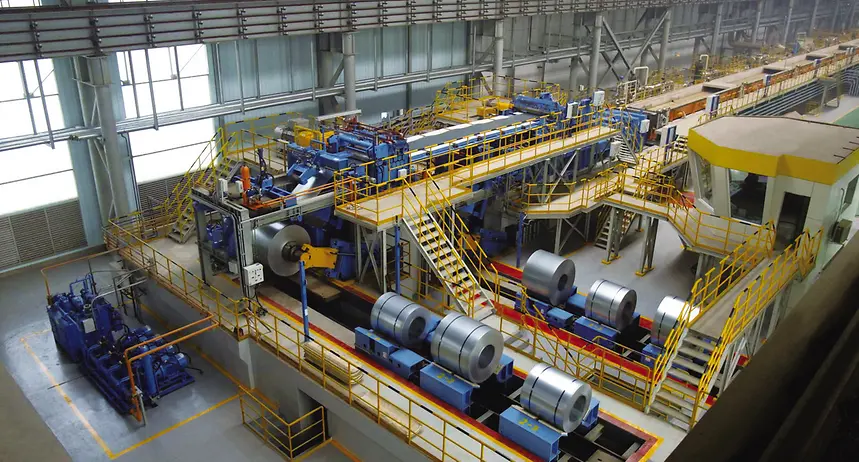
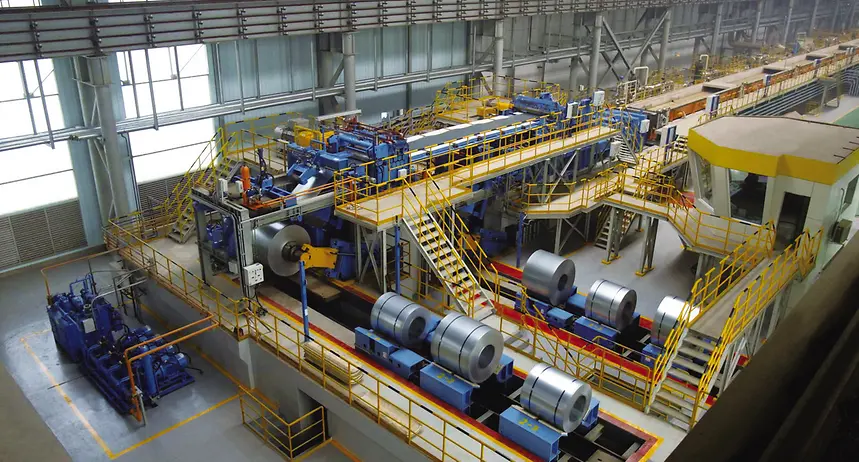
November 1, 2023
Inner Circle
Thermoplastic Valve & Piping Systems in Metal Finishing/Galvanization Applications
Contributed by Mark Gore, Business Development Manager (Marine, Metal Finishing, Power, Pulp & Paper, Railroad)
Recently, a Brazilian company asked Asahi/America for a recommendation on three chemical applications. The company produces metal sheets in a variety of materials and uses a galvanization process to galvanize its end product. The chemicals used in this process are: potassium permanganate, chrome hexavalent, and chrome trivalent. The company uses these to galvanize 316 stainless steel for their customers, and they are having ball valve issues related to said chemicals.
The application is in a low-temperature setting with a max pressure of 4 bars. The companies who sell the valves competing for this application were between a German and Brazilian company that cover ball valves and provide SST-lined valves.

The customer reach out to Asahi/America’s sales, engineering and business development teams to assess these applications and make appropriate material recommendations on valves.
Based on the application and request, here were Asahi/America’s material recommendations:
Potassium permanganate:
- PP – Not recommended
- PVC, PVDF – Good
- PTFE, FKM – Good
Chrome hexavalent:
- PP – Not recommended
- PVC, PVDF – Good
- PTFE (Best), FKM – Good
- EPDM – Not recommended
An example of a galvanization process assembly line at a steel mill.
Chrome trivalent:
- PP – Good
- PVC, PVDF – Good
- PTFE (Best), FKM and PTFE – Good
Key:
PP = Polypropylene
PVC = Polyvinyl chloride
PTFE = Polytetrafluoroethylene
EPDM= Ethylene propylene diene terpolymer
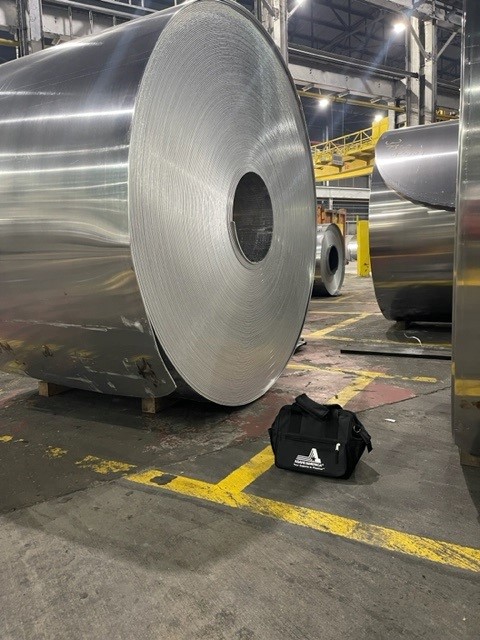
The Asahi/America technical services group added PVDF or ECTFE (Halar®) pipe as the recommended material for these process chemicals in this application. See below:
- PE100-RC and PP can be used up to 30° C, but the lifetime is limited to two to five years. In the case of the most minor mistakes in welding or installation, immediate failures cannot be excluded. IR welding is recommended to minimize stress.
- PVDF can be used up to 50° C with a maximum lifetime of five to ten years. In the case of the most minor mistakes in welding or installation, immediate failures cannot be excluded. IR welding is recommended to minimize stress. PVDF will turn brown.
- ECTFE (Halar®) is a recommended material up to 100° C, but Asahi/America’s technical teams need the concentrations in order to give a final confirmation. ECTFE (Halar®) will also turn brown but without significant influence on the material properties.
- FEP and PFA can be used without restrictions up to 150° C.
For any specific product application, please consult Asahi/America’s technical services department to determine the appropriate thermoplastic material given the chemical concentration. The recommendations in the above application story were specific to the application and customer’s specifications. Please consult Asahi/America for any application projects.
EDITOR’S NOTICE: Please note, the information in this article is for educational purposes only and does not supersede any Asahi/America technical information or product specifications. Please consult Asahi/America’s technical department at 1-800-343-3618 or pipe@asahi-america.com on all product applications in regards to material selection based on the pressure, temperature, environmental factors, chemical, media, application, and more.