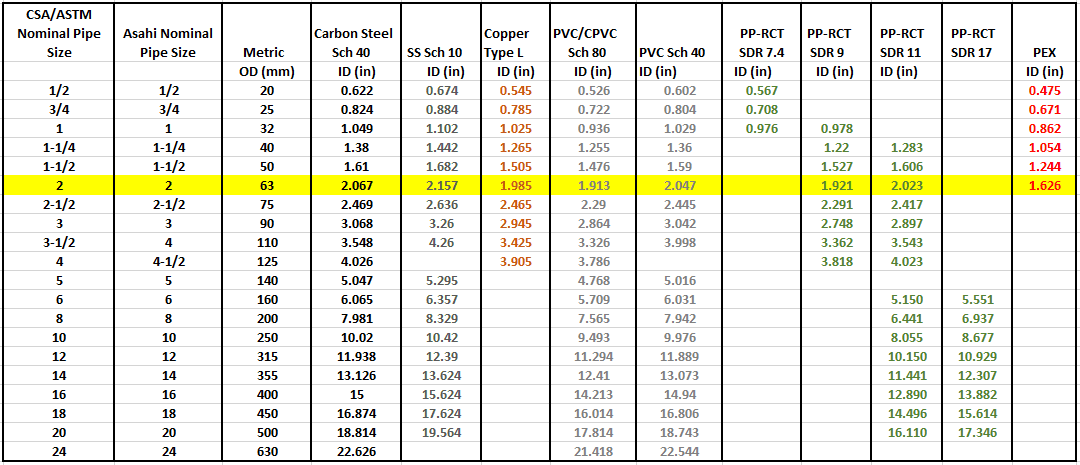
February 1, 2022
Inner Circle
Size Matters
Contributed by Rob Marsiglia, Industrial Piping Products Team Leader
We usually describe the different pipe classes and materials in very basic sizing terms (for example: ½”, 2”, 6”, schedule 40 or DR 11). Sometimes, we clarify by saying metric or IPS, but do we really appreciate the nuances of what we are saying? Do we really understand how the thickness, type of material, or even size, impacts the performance of a system?
The materials, classes, and construction all play significant roles in the critical characteristics of a piping system. They influence flow rate, velocity, and pressure drop.
If we use 2” carbon steel as the base reference, it has an inner diameter (ID) of 2.067”. For those who routinely work with steel pipes, this may be the baseline 2” pipe that you think of. However, you’ll see that all other materials listed, such as the schedule 10 stainless steel, copper, PVC, PP-RCT, and PEX. Each of these materials have different ID’s for the same 2” pipe size.
What’s the big deal? Well, if you choose another material for a particular application, instead of steel, then you need to know more than the nominal pipe size to judge flow rates, velocities, and pressure drops. Just saying 2” PVC doesn’t give you all the information you need. You still need to know if it’s a schedule 40 or schedule 80. Similarly, you need to know if PP-RCT is SDR 9 or SDR 11. In these cases, the wall thickness, adjudicated by either pipe schedule or SDR, will affect the ID and therefore the flow characteristics. For example, PEX tubing, has an ID of 2” but will the material be sufficient for the system requirements?
2” carbon steel has a H&W of 140. At a reasonable velocity of 5.75 feet/second, this provides 60 GPM flow, with a head loss of 6.4 feet/100 feet.
But, let’s look at this same pipe at lower H&W factors:
Let’s continue across our chart. We’ll assume a H&W of 120 for stainless steel and a constant H&W for thermoplastic pipes.
To put it all together:
What does this mean? It means that the variations have to be viewed against the backdrop of the system’s requirements and just calling it a 2” pipe without fully understanding what differentiates them, could hinder the progress of the entire structure.
For thermoplastic pipes, the ID is king. The schedule or SDR dictates the pipe’s ID and the performance characteristics are determined from there. Performance characteristics will stay constant for the life of the system often for 50 or more years, which is just one of many advantages of thermoplastic pipe.
The same cannot be said for steel pipes. Even stainless steel pipes have not had the same success that thermoplastic pipes have seen within various markets. If aging is not considered when selecting steel piping, how many systems can perform “like new” with a 56% increase in pressure drop over several years?
How critical are flow, pressure, and head loss? Tankless water heaters, automatic faucets and flush valves, glass washers, and autoclaves all have a specific supply range that needs to be maintained. Pressure drops that increase over time, as well as a nominal pipe size that results in higher pressure drops than expected, can adversely affect any system’s performance.
The effects of these variations are minimized, given the low flow requirements of modern plumbing fixtures. For example, it has been shown, PEX tubing, in ½” and ¾’ sizes, will perform equally as well as the same nominal size copper tubing in certain plumbing applications. This is primarily due to the minimal requirements of the plumbing fixtures in the system.
Automatic fixtures require minimum running pressures, which is a dynamic pressure/flow characteristic. This requirement becomes more critical in large facilities like stadiums, airports, office buildings, educational, and institutional facilities where multiple fixtures of various types might be operated simultaneously. For example, an automatic flush valve usually has a 25psig minimum requirement. Although this may seem easily achievable, it is not just about the pressure, but also about the minimum flow requirement (usually 1.6 GPM) needed for a functioning system. In large-use facilities, this dynamic condition needs to be applied across multiple valves (and fixtures) at the same time and sometimes on multiple levels.
These large systems have substantial pipe runs and even a small change in head loss, multiplied over hundreds (if not thousands) of feet of pipe can make a negative impact on fixture performance as well as user experience.
Asahi/America offers a diverse range of thermoplastic piping materials with a wide array of wall thickness to accommodate chemical, commercial, industrial, environmental, and high purity applications. We can help guide you through the maze of IPS, metric, schedules, and SDR sizing to help keep your structures’ flow characteristics consistent for the life of the system.
EDITOR’S NOTICE: Please note, the information in this article is for educational purposes only and does not supersede any Asahi/America technical information or product specifications. Please consult Asahi/America’s technical department at 1-800-343-3618 or [email protected] on all product applications in regards to material selection based on the pressure, temperature, environmental factors, chemical, media, application, and more.