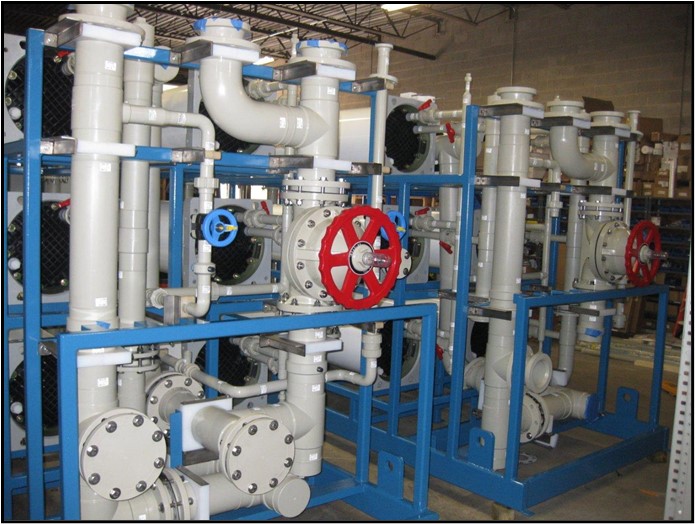
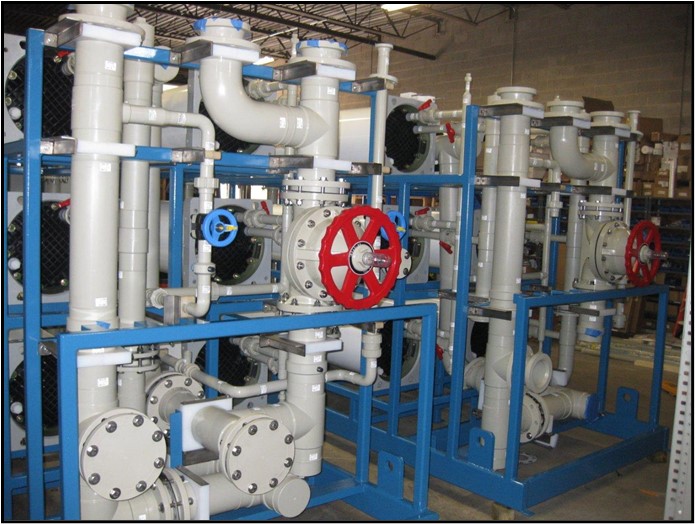
February 1, 2024
Inner Circle
Polypropylene Pipe Applications in the Power Industry
Contributed by Mark Gore, Business Development Manager
For many applications, steel pipe is the solution, especially in power plants where pressures and temperatures exceed thermoplastic pipe’s pressure and temperature limits. There are some exceptions to this unwritten rule, and for this article, we will discuss a few of these applications where polypropylene pipe works exemplarily in the correct application.
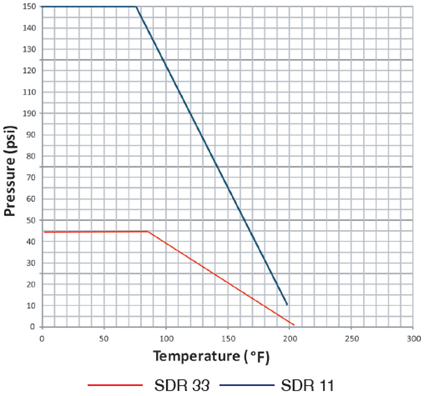
Polypropylene (PP) is a resin material suitable for a wide range of applications with a pH range from 1 to 14 and at temperatures that just exceed 200° F. Pipe sizes range from 1/2″ to 48″ in SDR 11, 150psi rated and from 4″ to 55″ SDR 33, 45psi rated. PP is also offered in SDR 17, 90psi rated.
One manufacturer—Borealis—classifies their PPr as RA130E-8427, DIN 8078, and DIN 8077. RA130E-8427 is a high molecular weight, random copolymer resin that exhibits a high weld strength, impact resistance, and faster relaxation due to a lower modulus of elasticity. This material is suitable for recycling using modern recycling methods.
To put this into perspective, here are three typical hot water applications:
Application 1:
- P1: 40psi
- T1: 170° F
- LN: 3″
- SG: Boiler pre-heat water coming off the de-aerator and then being sent back to the boiler water tank.
- Expected life span for PP pipe: Heat aging limits the pipe life to a maximum of 16 years, allowing for 63psi with water. In chemical applications, 42psi is the max operating pressure. The short story is the pipe will fail from heat fatigue before pressure is an issue. This outcome is actual for both PPR and PPH.
Examples of single wall and double wall PP piping systems.
Application 2:
- P1: 50psi
- T1: 190° F
- LN: 2″ to 6″
- SG: Boiler condensate return water going into pre-heat clean water tanks to bring water temperature up to proper temperature.
- Expected life for PP pipe: Heat will limit the pipe’s expected life to no more than seven years at a maximum of 50psi. Heat will cause failure at ten years, so even if the pressure is lowered, it will not increase life expectancy. In this case, there is no significant difference in PPR vs PPH.
Application 3:
- P1: 35psi
- T1: 45° F
- LN: 2″ to 4″
- SG: Fresh water just filtered and starting the pre-heat cycle.
- Expected life span for PP pipe: Full life expected (50 years up to 124psi). Given the very low pressure in this application, the pipe will be well-suited.
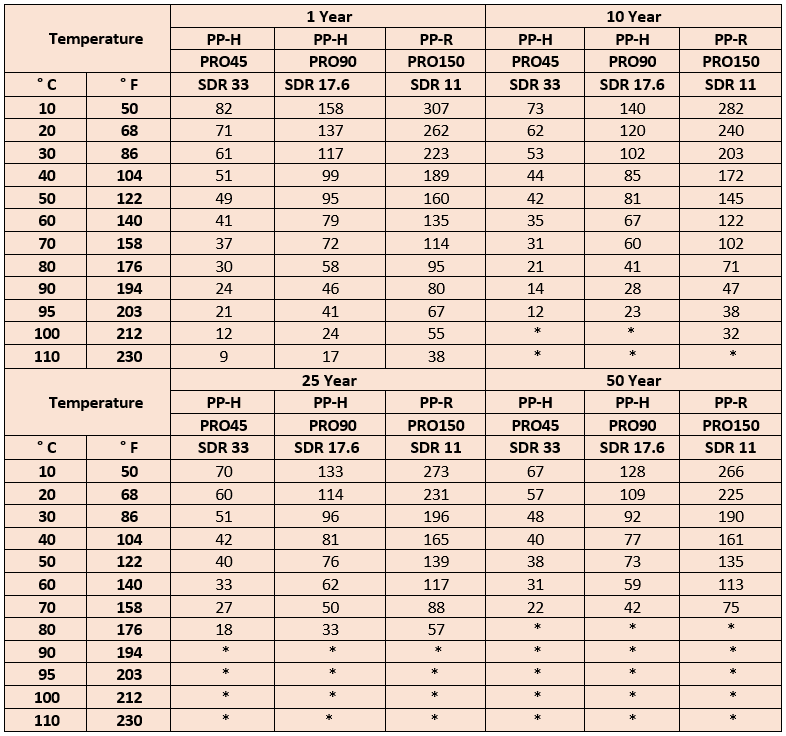
As you can see from these three examples, the life expectancy of polypropylene pipes varies based on the pressure-temperature of each application. A good rule of thumb with thermoplastic pipe applications is that the higher the temperature of the application, the lower the pressure should be.
Based on the estimated years of life span, this application could give the end user a longer-than-expected pipe life than metal pipe. The PPr pipe does not rust or gather calcium deposits in the inner pipe wall due to its Hazen-Williams number value of 150 for the ID surface finish.
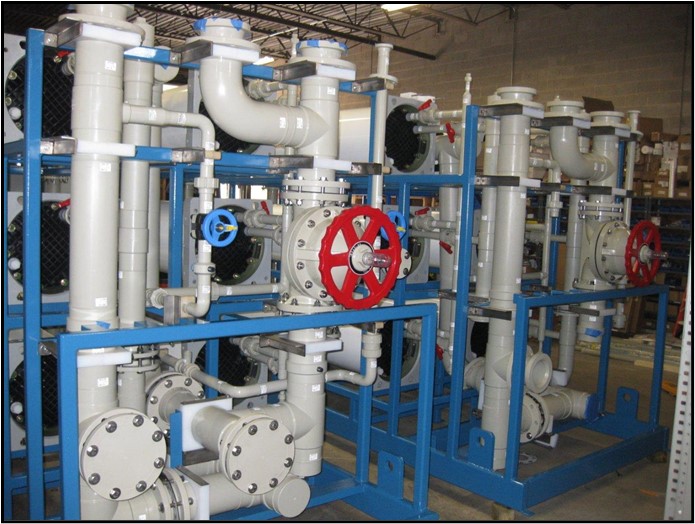
Chemicals in water treatment can be a constant issue for metal piping as they can chemically attack the metal pipe, causing pitting, scale, and pinholes, which potentially cause environmental issues. Typical chemicals used for water chemical treatment applications include:
- Sodium Hypochlorite (Bleach) — PE100-RC or PP up to 3mg/L with a max temperature of 104° F for PP.
- Corrosive Chemicals (Alkalis) — PP works excellent.
- Organic Solvents (Lyes) — PP that does not work well for high concentrations or high temperatures can be used for drainage applications.
- Strong acids & aqueous caustics — PP works well up to 80% concentrations and is conditional at any concentrations above 80%.
- Hydrochloric and Hydrofluoric Acids — PP works well for 20% and 40% concentrations, respectively, due to acid diffusion.
Polypropylene works well for each of these types of chemicals based on pressure/temperature conditions for the PP piping material. As detailed above, Sodium Hypochlorite (bleach) would work best with PE100-RC material.
As with all chemical applications, consultation with your pipe supplier is necessary for proper material selection based on the application and estimated life expectancy. PVDF or ECTFE might be the better option in some applications where PP pipe is not good.
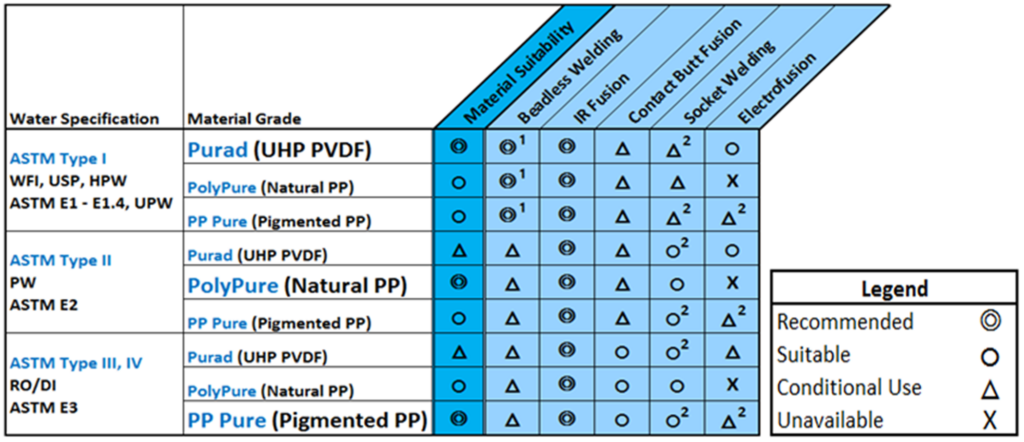
Ultrapure deionized (DI) water and reverse osmosis (RO) water systems are additional application opportunities for PP pipe. One of the issues with DI and RO water systems is maintaining the resistivity (Ohm rating) once the water leaves the system. Many installations use PVC, CPVC, or even carbon steel pipe for their DI or RO water piping systems. But what happens when you deionize water? To deionize, you remove ions from the water, after which the water constantly looks to replace the ions it has lost; in these cases, it will do so from the pipe environment around it. “Leach out” describes this phenomenon when DI water leaches material out of the inner diameter pipe wall as it tries to replace its missing ions, and is the number one reason you want to select the proper piping material for your system–otherwise, you risk contaminating the media within the pipe. If you spend $50,000, $75,000, or $100,000 on a DI water system to have an Ohm-rated water value of “X,” your piping system should give you the Ohm rating you paid to have installed.
The second most significant issue with non-PP pipe is that you have areas for stagnant water to form. Stagnant water can create bacteria and cause damage to your water rating. These are critical factors to consider when properly selecting your piping system for the DI or RO water piping system. PP is an excellent replacement for PVC, CPVC, or WCB pipe; consult your ASTM, ASME, USP, TOC, Resistivity, TDS, and bacteria guidelines for more details.
There are many ways of adequately fusing polypropylene pipe—two common techniques are butt fusion and socket fusion, compared to a solvent cement option or a metal welding option for PVC/CPVC and metal pipe. By fusing pipe together, you can eliminate potential leak zones by heating the material to a molten state, then pushing it together with force and holding it in place until cooled. Thus, you have created a weld bead stronger than the actual pipe. Other ways to fuse PP pipe include IR fusion (non-contact), beadless fusion, and electrofusion welding.
These five fusion examples will give you a better understanding of how to fuse PP pipe. Each has its own benefits and ideal environments, but the ultimate decision for proper welding method is based on your process requirements. Infrared (IR) fusion and beadless fusion are typical for pharmaceutical and silicon chip processes, while butt, socket, and electrofusion are typical for industrial environments.
Whether you are looking at boiler feed water, boiler chemical treatment system, water pre-heat system, DI water, or an RO system, polypropylene is an excellent alternative to metal piping systems in power plants. Remember that only some applications are high temperature and high pressure, so it can be beneficial to look at other options for your power water applications.
EDITOR’S NOTICE: Please note, the information in this article is for educational purposes only and does not supersede any Asahi/America technical information or product specifications. Please consult Asahi/America’s technical department at 1-800-343-3618 or pipe@asahi-america.com on all product applications in regards to material selection based on the pressure, temperature, environmental factors, chemical, media, application, and more.