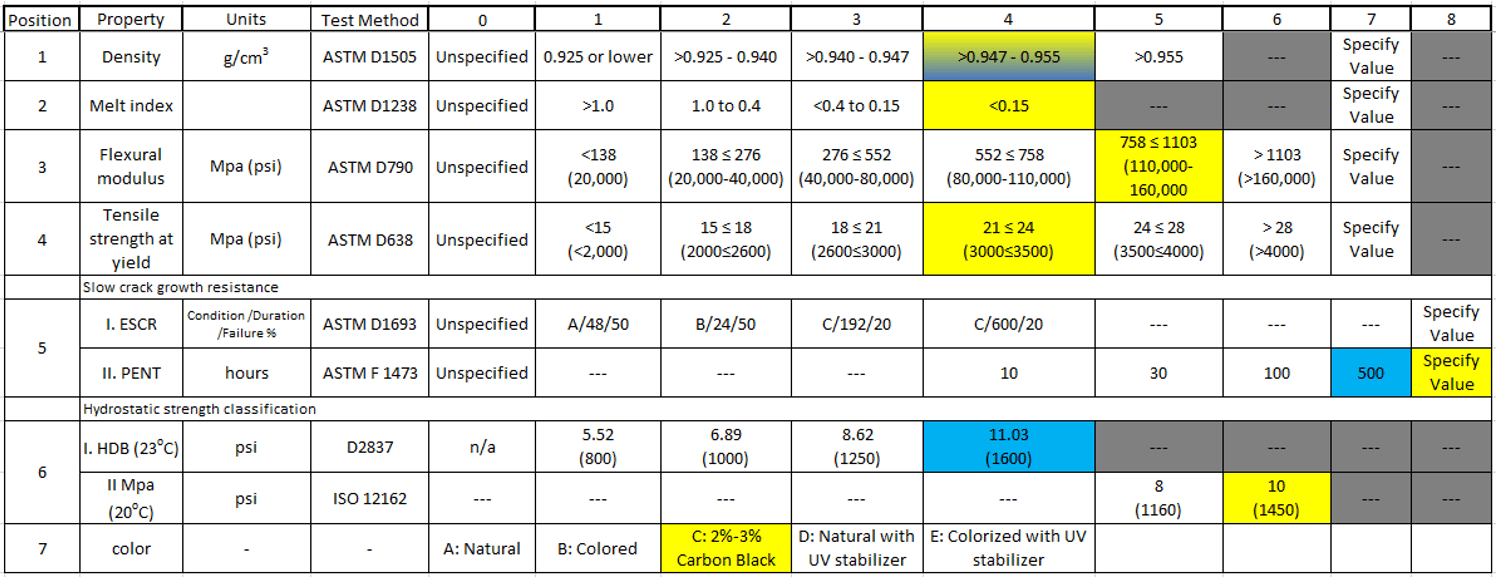
February 1, 2023
Inner Circle
Polyethylene: How Many Names Can One Product Have?
Contributed by Joshua Goldberg, Business Development Manager
Plastics—it’s all the same, right? In my last article, we saw that that statement is not necessarily true, and many high-performance polymers fall under the “plastics” moniker. This article will concentrate on one of the most common polymers, polyethylene, and unlock the mystery behind its confusing, convoluted naming scheme.
Polyethylene first came about in the 1930s from Imperial Chemical Industries, but this material’s makeup was highly branched, creating LDPE (low-density polyethylene). Additionally, the material was made under high-pressure conditions, around 20,000 – 30,000psi. Shortly after LDPE’s creation, a process was discovered that could create a more linear molecule under pressures of only about 100psi. It took almost 20 years before Paul Hogan and Robert L. Banks at Phillips Petroleum Company discovered the chromium catalyst to make HDPE (high-density polyethylene) that is responsible for jumpstarting the polyethylene industry. Today, there are many different types of polyethylene on the market, so there is a need to give this material a designation that will help people differentiate between the polyethylene that makes up high-performance chemical pipes and the polyethylene that you wouldn’t want to use in pressurized situations. Designating polyethylene (PE) is convoluted and not globally consistent, and there are several different naming conventions depending on how specific you want to get about the material. So, when considering PE, what’s in a name? For the sake of brevity, the PE referred to in the rest of this article will be HDPE used for the chemical piping industry.
Let’s start with the most commonly recognized name on the international marketplace, PE100. This designation expresses the long-term strength of the PE material that makes the pipes, and its an ISO designation. In the case of PE100, the pipe’s raw material has a Minimum Required Strength (MRS) of 10MPa at 20°C for 50 years as per ISO12162. So, PE80 would have an MRS of 80MPa at 20°C for 50 years, PE63 would be 63MPa, and so on. So, the designation of PE100 is quite vague since this is the minimum requirement for the material that makes the pipes. For the rest of the article, we will be referring to the PE100 group of materials as we try to detangle ASTM D3350 and its attempt to differentiate the properties behind the actual pipes.
ISO is the standards system used by most of the rest of the world, whereas the United States relies on ASTM. Due to rapid advances in PE manufacturing processes overseas and domestically, ASTM developed a naming convention to compare different PE grades more easily. Below is the latest chart from ASTM D3350. Let’s look at how this applies to names like PE4710 and PE445486C.
PE445486C is highlighted in yellow above, and PE4710 is highlighted in blue. I call out these two names specifically because PE4710 are pipes manufactured with PE100 material domestically, while PE445486C are pipes manufactured with PE100 material in the EU. First, let’s address the difference in the numbers in the designations. PE4710 is an abbreviated name for the material’s typical designation of PE445574C, and the “10” comes from multiplying the HDB (position 7) by a service factor of 0.63 (ex. 1600psi x 0.63= 1008, the “08” is dropped to get the number 10). It all seems straightforward until we consider the PE445486C European PE.
There are two critical areas where we should take note of a direct comparison between PE4710 and PP445486C. The first area to note is Row 5 on the chart. PE445486C falls under the specify value category, while PE4710 registers at 500 hours in the PENT test. The PE445486C used to make Asahi/America’s Chem Proline® pipes registers at over 16,000 hours in the same PENT test! The vast differences between the two materials in that position alone have caused ASTM to look at further updates to better keep up with PE technology advances.
The second area of note is Position 6 on the ASTM D3350 chart. Test I. HDB is based on ASTM D2837, whereas Test II. Mpa is based on ISO 12162. The tests are two very different tests! No conversion factor can be applied to compare the materials directly, and there’s no reconciliation between the two tests on the horizon. So, we are left with a naming convention that everybody uses globally, but it only provides a fair comparison for domestic PE. Additionally, since the rest of the world uses the ISO system, we will only be able to get an honest comparison between domestic and foreign PE sometime soon if something is done to rectify the differences between the two test methods. Luckily, several committees are looking at this very problem, so there is a chance that there may be some consistency soon. Asahi/America is committed to the advancement of thermoplastics and has several subject matter experts who volunteer on committees like Plastic Pipe Institute (PPI), ASME, ASTM, and more. If you are interested in volunteering your time to help advance thermoplastics on one of these committees, reach out to learn more.
The world of polyethylene has been rapidly changing since its inception, so it has been hard to keep up with standardizing all the changes in the material. Additionally, now that improvements in the material are being made globally, there is a need to be able to compare all the materials on the market directly. ASTM has made a good attempt at categorizing the differences, but there is still room for improvement in the system. With the vast difference between Chem Proline® (PE445486C) and PE4710 in the Slow Crack Growth Resistance PENT test (Position 5) already warranting another round of editing, perhaps the next iteration of ASTM D3350 will finally be able to reconcile the differences in US standards and those of the rest of the world.
EDITOR’S NOTICE: Please note, the information in this article is for educational purposes only and does not supersede any Asahi/America technical information or product specifications. Please consult Asahi/America’s technical department at 1-800-343-3618 or [email protected] on all product applications in regards to material selection based on the pressure, temperature, environmental factors, chemical, media, application, and more.