Page Category: Check Valves
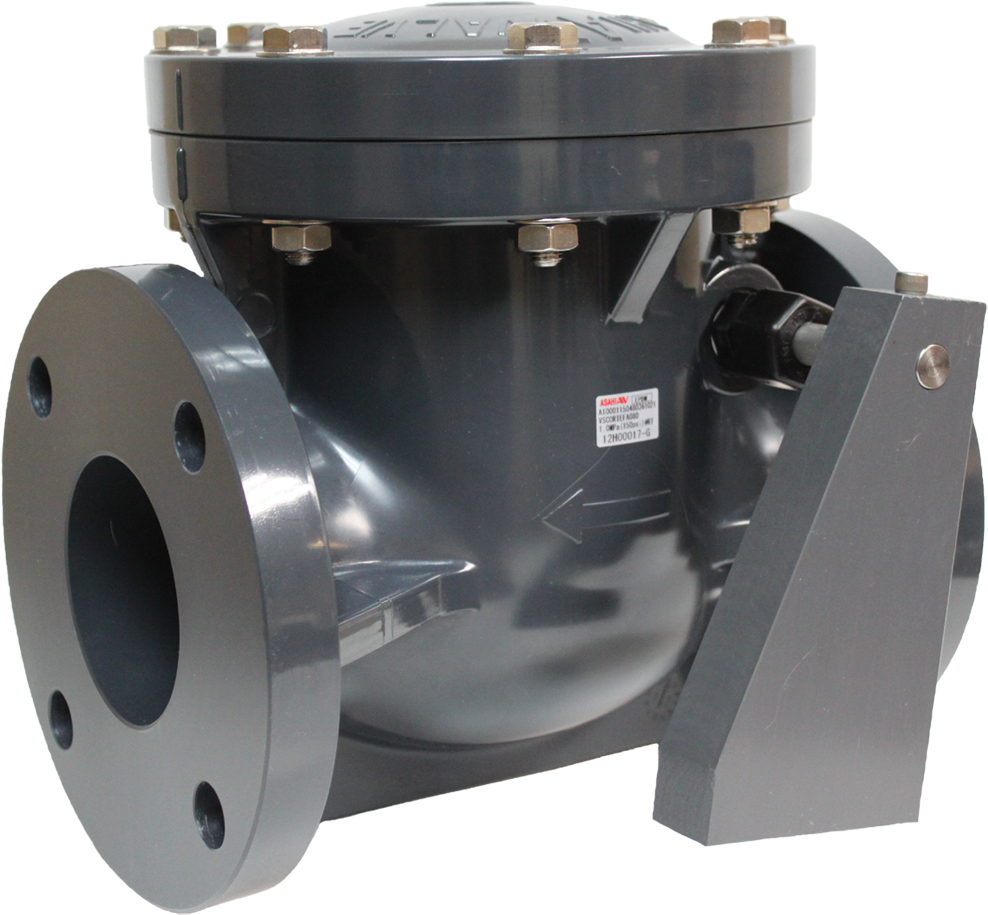
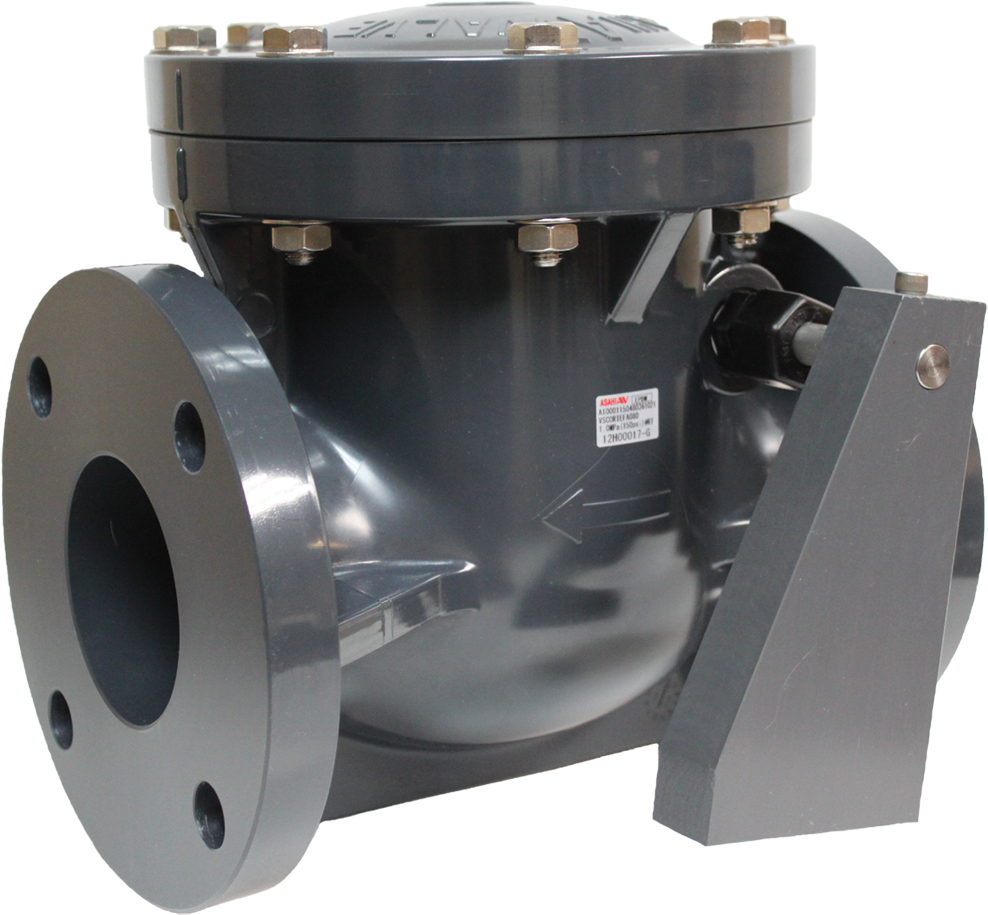
Page Category: Check Valves
Swing check valves have the option to install an external spring assist assembly. This spring is made from 316 stainless steel and is mounted external to the valve. When fluid pressure starts to drop, the spring retracts the swing arm and brings the disc back into the seat position. This effectively reduces the speed of the fluid flowing back towards the check valve, reducing the shock caused by water hammer. The spring returns the disc to the seat, but does not accommodate sealing. Hence, minimum backpressure requirements still apply for swing check valves with spring assists.
The lever and weight assembly for swing check valves achieve the same function as a spring assist. The exception is that the closing action is provided via a weight connected to the swing arm of the valve. Because lever and weight assemblies rely on gravity to provide their assistance on a closed stroke, they tend to work better in vertical installations.
Ideal Applications Include:
Water hammer reduction In the following industries: Chemical processing, bleach plants, aquariums, mining, water treatment, landfills, swimming pools, power plants
Specifications:
Sizes:
3/4″ – 8″ Swing check valves
Bodies:
PVC, PP, PVDF
Seals:
EPDM, FKM, PTFE
Shafts:
316 stainless steel
Spring:
316 stainless steel
Counterweight:
PVC
- Prolonged piping service life
- Low cracking pressures
- Installs in either the vertical or horizontal position
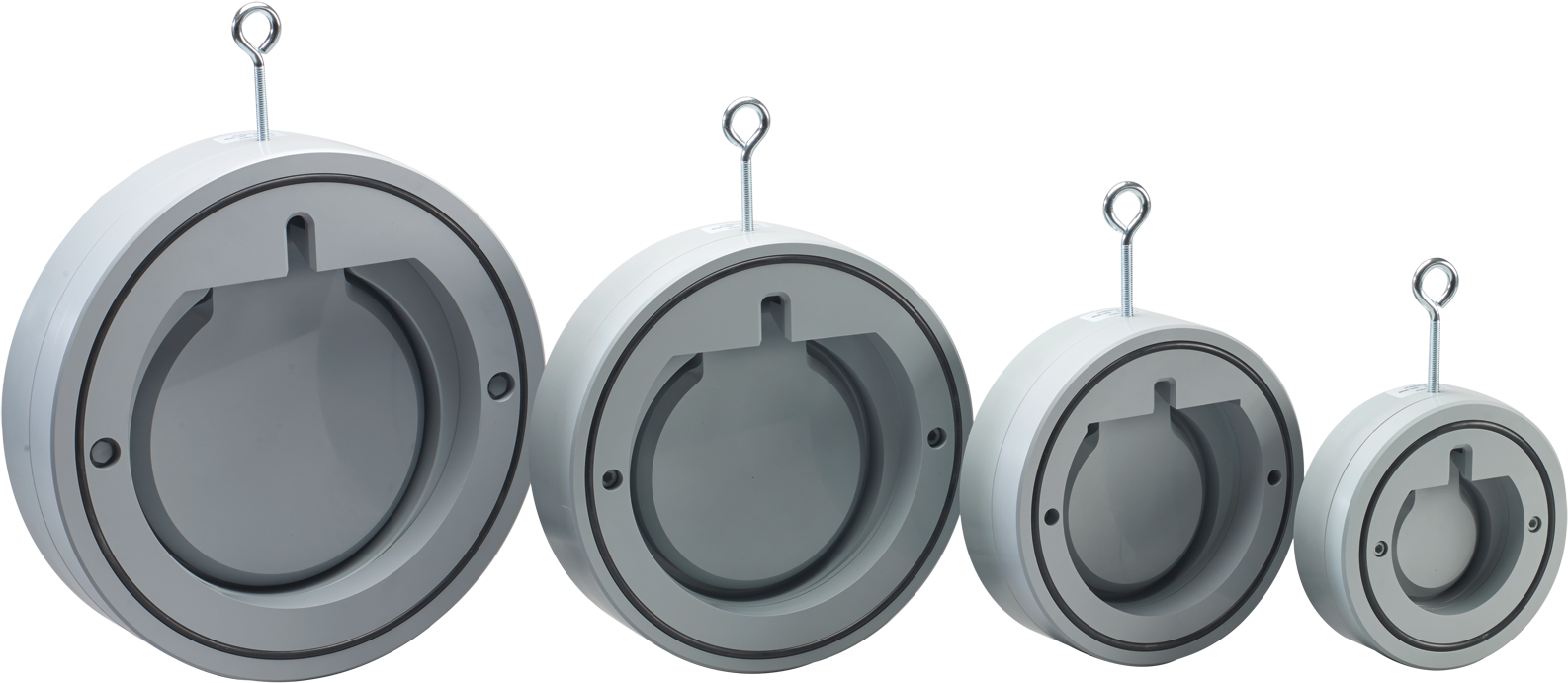
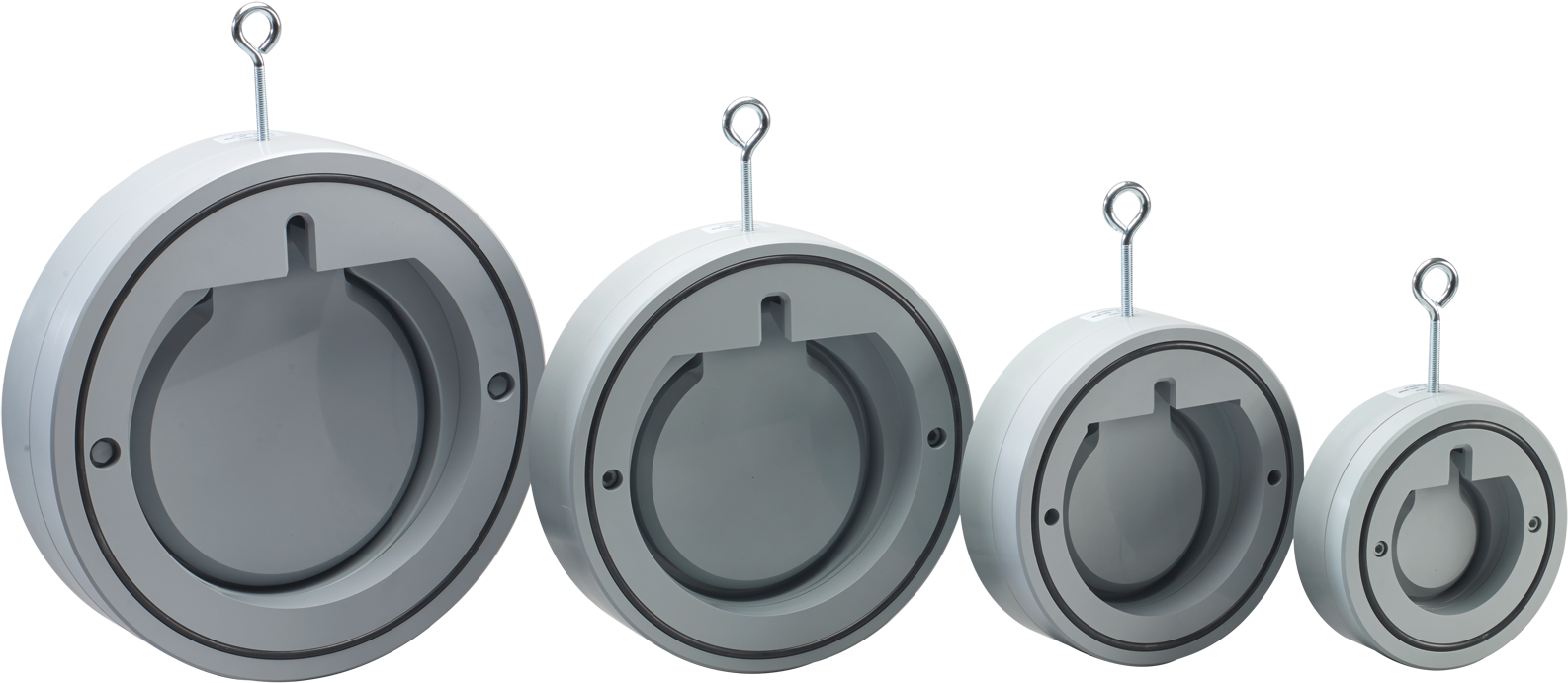
Page Category: Check Valves
Wafer check valves have a solid thermoplastic body with a very thin “wafer” profile that makes them an ideal check valve for applications that require valves with short takeout lengths. Similar in operation to a swing check valve, the wafer check has a solid thermoplastic disc and seat arrangement that performs the check action. In one direction, fluid lifts the disc off of the seat and allows fluid to pass freely. In the opposite direction fluid drives the disc into the seat, creating a seal and preventing fluid from back flowing upstream. Because of its slim profile, wafer style checks are unlikely to clog, which makes them ideal for service lines with large debris or solids. Wafer check valves are used in applications where it is essential to ensure fluid flow passes in only one direction. Wafer check valves can be mounted in vertical or horizontal directions, with the only restriction being a minimum back-pressure required to properly seat the check valve. Spring assists and lever and weight mechanisms are available options to assist in closing the valve quicker to reduce water hammer concerns.
Resources:
Data Sheet
Ideal Applications Include:
Tank inlets/outlets, preventing backflow into a pump, one-way mixing, water hammer mitigation, pressure balancing, process intakes.
In the following industries: chemical processing, bleach plants, aquariums, mining, water treatment, landfills, swimming pools, power plants
Specifications:
Sizes:
3” – 12”
Models:
Wafer style ANSI
Bodies:
PVC
Seals:
EPDM or FKM
- All 3″ – 8″ wafer check valves operate at a maximum pressure of 150psi, 10″ and 12″ valves at 90psi and up to 120° F
- PVC body with EPDM or FKM seals
- Slim profile permits easy installation
- Wafer style fits between two-mating flanges
- Face-to-face meets ASME/ANSI B16.10
- No spacer required
- No pipe interference with disc
- No bolt pattern: permits installation using ANSI/JIS/DIN mating flanges
- Vertical or horizontal installation
- No external shaft
- Excellent chemical resistance
- Stainless steel external spring assist (ECTFE coated in 316 stainless steel) for 4″ – 12″ wafer check valves
-
Wafer check valves have the option to install a spring assist mechanism in the valve. This spring can be made from either 316 stainless steel or 316 stainless steel with a coating of PTFE for additional chemical resistance. When fluid pressure starts to drop, the spring pushes the ball back into the seat before the fluid stops and reverses direction. This will reduce the speed of the fluid flowing back towards the check valve, minimizing the shock caused by water hammer. The spring assist assembly does not accommodate sealing. Hence, the minimum backpressure requirements still apply for wafer check valves with spring assist assemblies.
-


Page Category: Check Valves
Swing check valves have a solid thermoplastic body with a large “flapper” that seats against the body of the valve. Swing check valves offer a large fluid area with a removable bonnet that allows for the valve body to be cleaned out without removing the valve from the pipeline. This is beneficial for installations that may contain debris or other items that could potentially clog the valve. Check valves are used in applications where it is essential to ensure fluid flow passes in only one direction. Check valves can be mounted in vertical or horizontal directions, with the only restriction being a minimum back-pressure required to properly seat the check valve. Spring assists and lever and weight mechanisms are available options to assist in closing the valve quicker to reduce water hammer concerns.
EL-PVDF Swing Check Valve
Asahi/America also offers the EL-PVDF swing check valve option. The EL-PVDF swing check valve for use in electrolysis plants in high temperature sodium hypochlorite, chlorine gas, brine, and hydrofluoric acid applications. The purpose of the EL-PVDF material is to prevent the generation of blistering or cracking that can occur in conventional PVDF during electrolysis production. EL-PVDF has been designed to achieve 2-5 times the normal life expectancy when compared to conventional PVDF in electrolysis applications. EL-PVDF performs in the most severe working conditions. Valves that are continually exposed to near maximum material working temperature limits for extended periods of time, especially in the production of chlorine, are the intended application target. Typical applications include, chlorine manufacturers, steel pickling lines, and pulp and paper manufacturing.
Resources:
Data Sheet
Specifications
- Specification – Swing Check Valves
- Specification – EL-PVDF Swing Check Valves
- Specification – Swing Check Valves for Landfill
Ideal Applications Include:
Tank inlets/outlets; preventing backflow into a pump; one-way mixing; water hammer mitigation; pressure balancing; process intakes. In the following industries: chemical processing, bleach plants, aquariums, mining, water treatment, landfills, swimming pools, power plants
Specifications:
Sizes:
3/4″ – 8″
Bodies:
Hi-PVC, PP, PVDF, EL-PVDF
Seat & Seals:
EPDM, FKM, PTFE
Models:
Flanged Connection Only
- Minimum flow resistance – low pressure drop
- Horizontal or vertical installation
- All sizes rated for full vacuum service
- Minimum back pressure to seat disc tightly
- Top access cover facilitates maintenance without body removal from pipeline
- All thermoplastic body
- All PVC parts made of high impact PVC
- PVC and PP valves come with EPDM seals (part #’s 5j, 5k, 6 and 7) as standard
- PVDF valves, part #’s 5j and 7 of PTFE and 8 of PTFE/PFA
- 3/4″ PP valves supplied with Ring 1a
- Assist Assemblies
- PTFE or FKM Seat and O-Rings
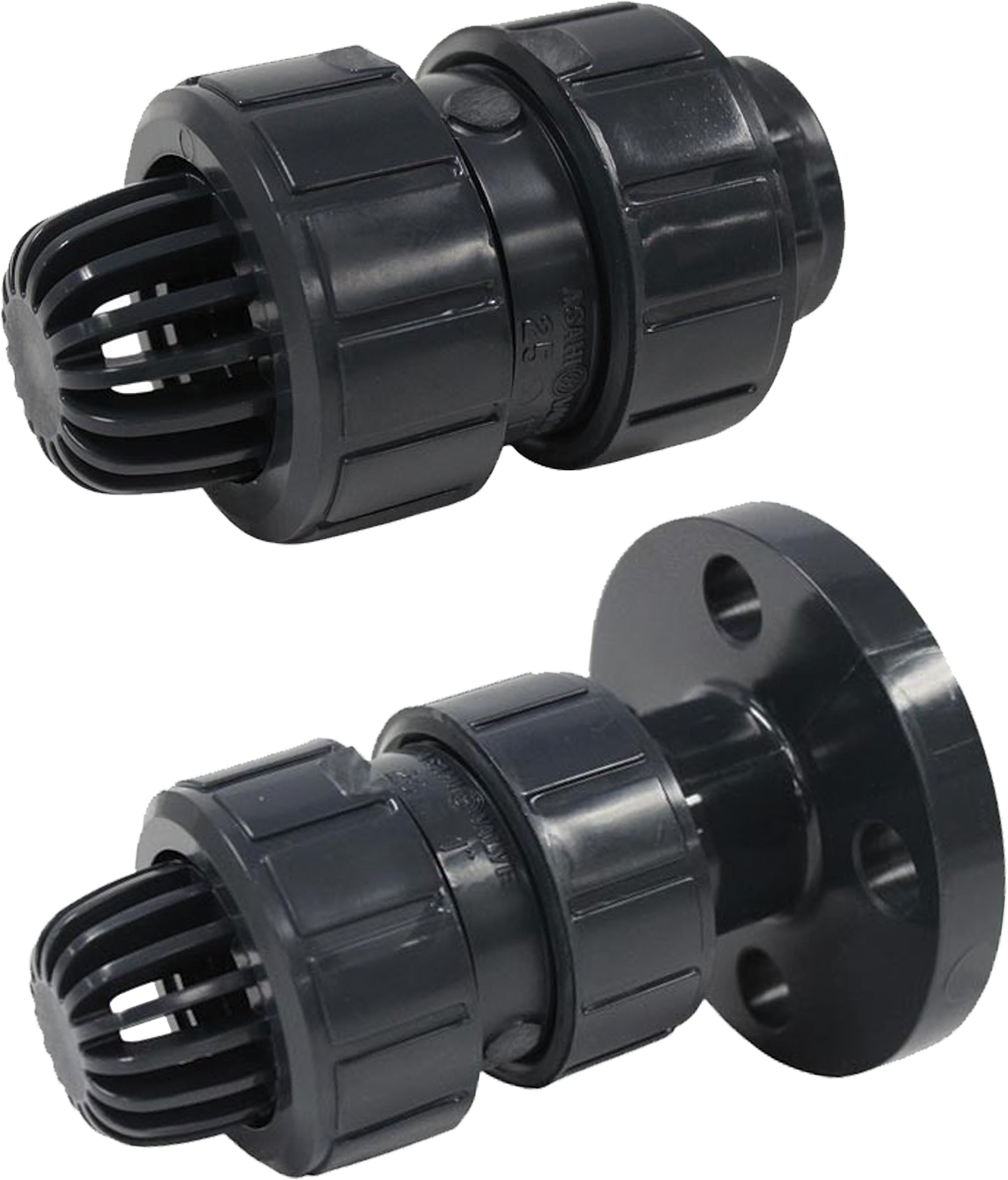
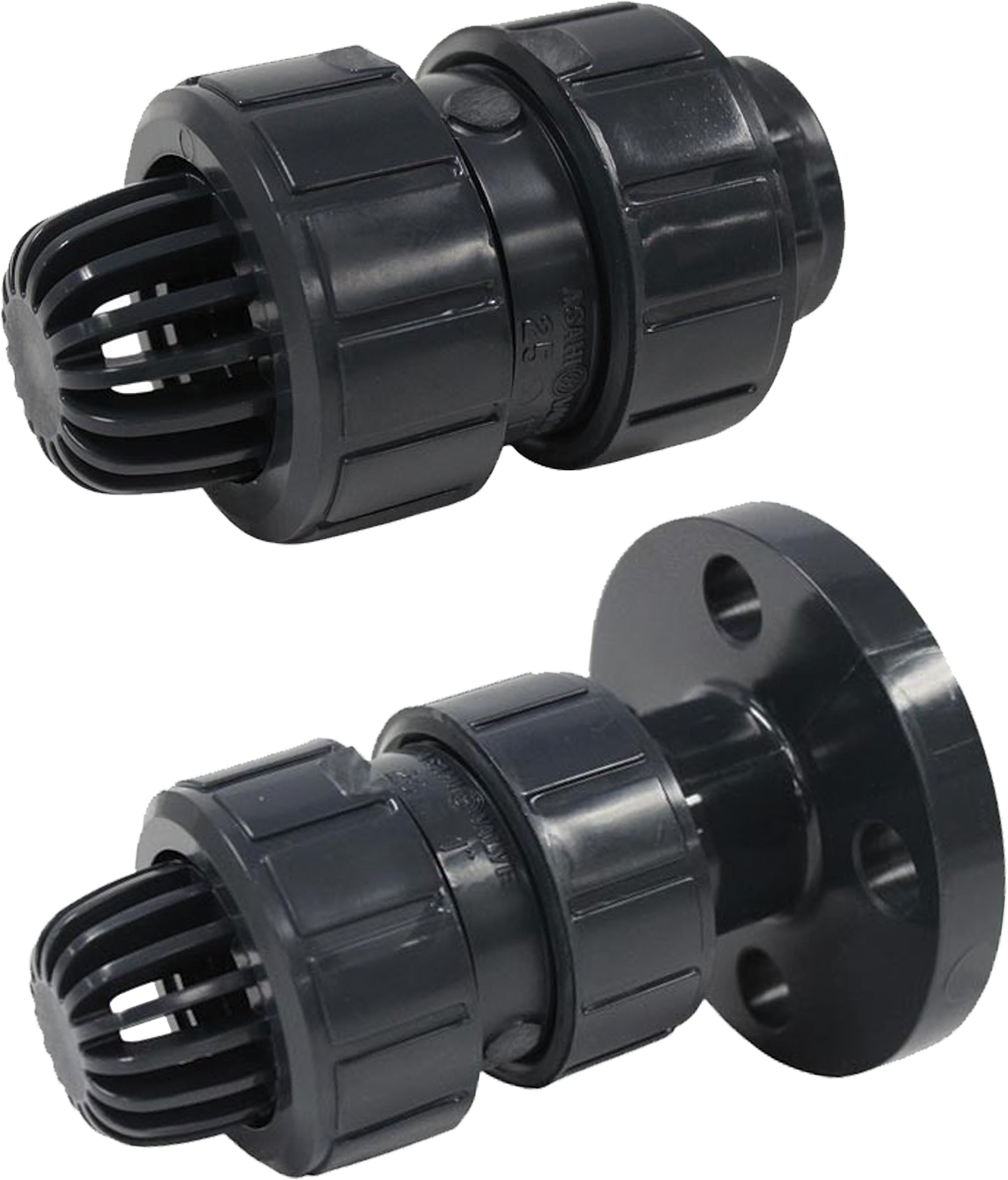
Page Category: Check Valves
A ball check valve with a foot screen can be installed vertically or horizontally on the suction side of a pump. The foot valve is an optional ball check valve arrangement where a screen is fitted into the inlet end of a ball check valve. This screen is used to filter large debris and solids from a fluid to prevent damage to pumps, clogging of valves and to protect downstream instrumentation. Foot valves can be typically found anywhere there is a check valve used as an intake. This includes pump inlets, lift stations and drains.
Resources:
Data Sheet
Ideal Applications Include:
Chemical Processing, Water & Wastewater, Landfills, Irrigation, Food Processing, Mining
Specifications:
Sizes:
True Union: ½” – 2″
Single Union: 3″ – 4″
Bodies:
PVC
Seals:
EPDM, FKM
Models:
Socket, Threaded, Flanged (ANSI), Butt End
Seats:
EPDM, FKM
Options:
Screen Options: PVC, CPVC, PP, PVDF
- Uniseat/seal of EPDM or FKM
- Ball is the only moving part. It unseats to permit flow in one direction but seals against seat to prevent backflow.
- May be used vertically or horizontally
- Minimum shut-off of 5psi
- All sizes rated for full vacuum service
- Solid thermoplastic ball
- Serves as a pre-strainer for large debris
- Installs in existing valves
- Screens available in a variety of thermoplastic materials
- PTFE coated FKM uniseat/seal
- Spring-loaded ball to assist ball in seating faster
- Screen options: PVC, CPVC, PP, PVDF


Page Category: Check Valves
The Asahi/America ball check valve employs a free moving ball, which unseats to permit flow in one direction, but seals against a seat to prevent backflow. It may be installed vertically or horizontally. Also available as foot valve for suction side of pump.
Resources:
Data Sheet
Specifications
Ideal Applications Include:
Chemical processing, bleach plants, aquariums, mining, water treatment, landfills, swimming pools, power plants
Certifications:
Specifications:
Sizes:
True Union: 1/2″ – 2″
Single Union: 3″ – 4″
Bodies:
PVC, CPVC, PP and PVDF
Seals:
EPDM, FKM, PTFE
Models:
Socket, Threaded, Flanged, Butt End
Seats:
EPDM, FKM, PTFE
- Uniseat/seal of EPDM or FKM
- Ball is the only moving part. It unseats to permit flow in one direction but seals against seat to prevent backflow.
- May be used vertically or horizontally
- Minimum shut-off of 5psi
- All sizes rated for full vacuum service
- Solid thermoplastic ball