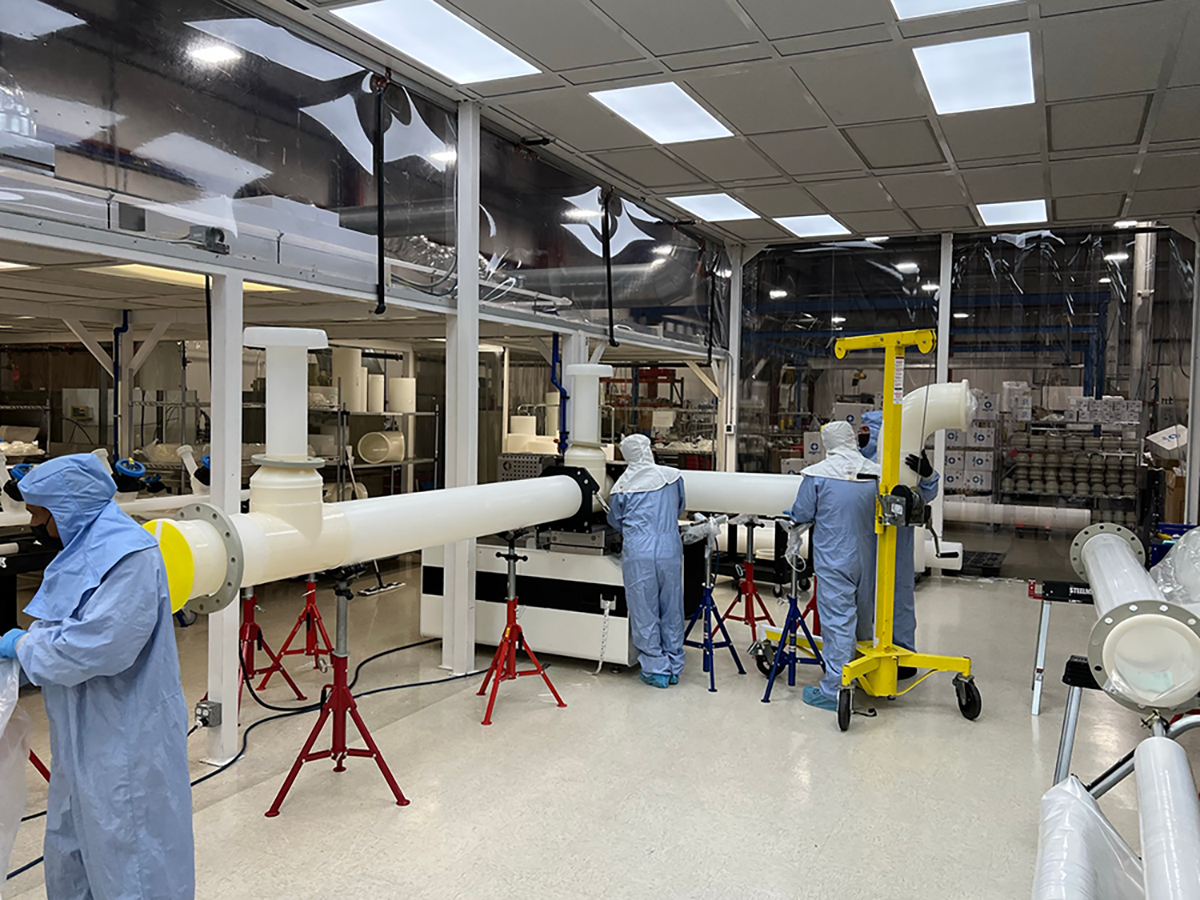
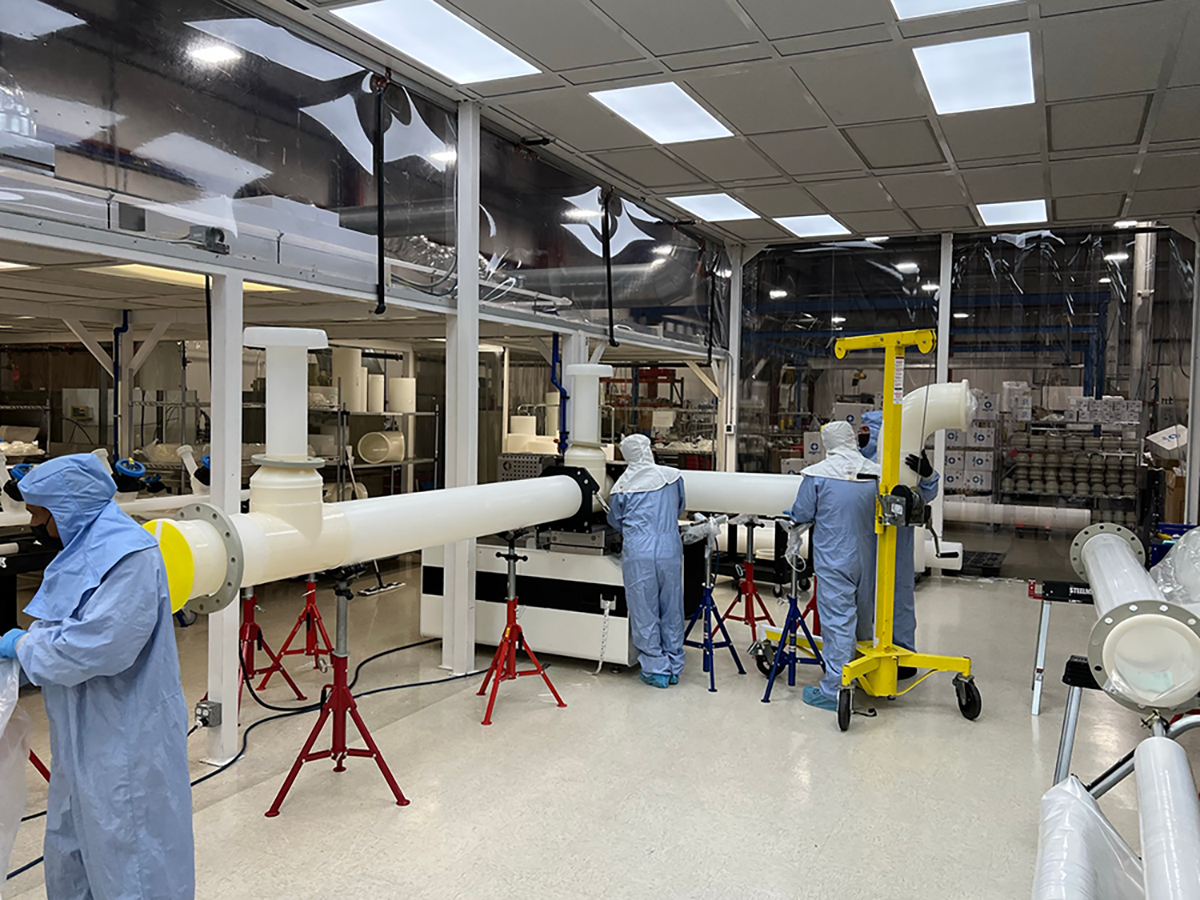
November 1, 2023
Inner Circle
Overcoming Challenges of Off-Site Manufacturing
Contributed by Mike Willen, High Purity Team Manager
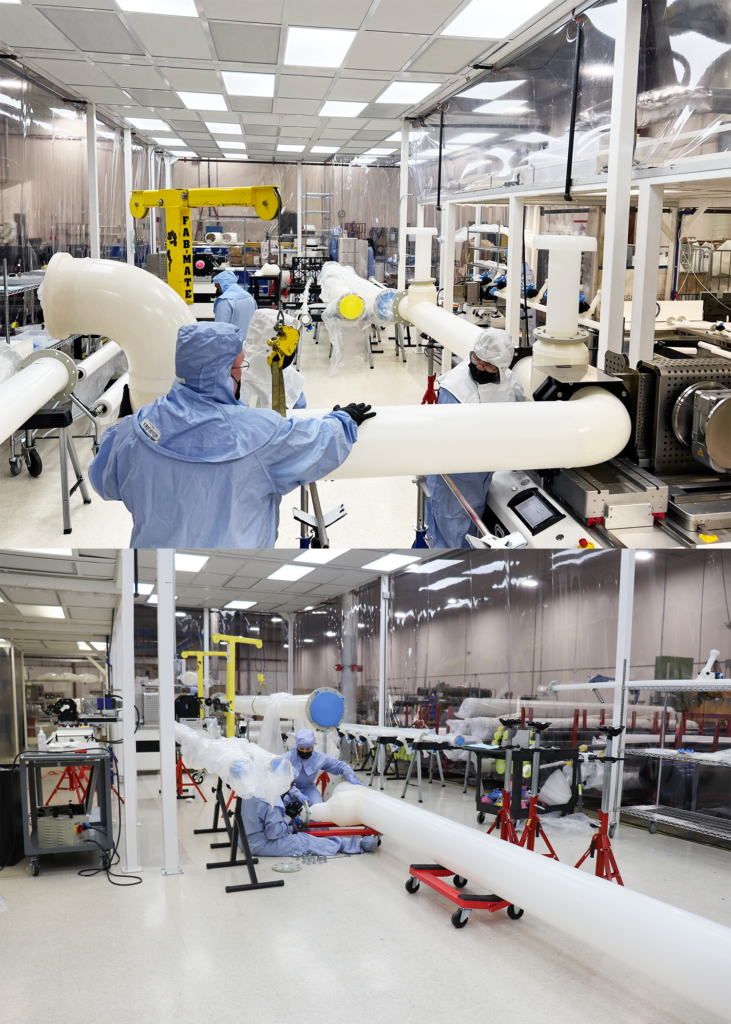
The number of new semiconductor fabs being built in the U.S. has reached an unprecedented high. Shortages of on-site skilled labor are pushing the industry to adopt off-site manufacturing (OSM) and modularization strategies. While there are many advantages of utilizing an OSM approach, it also introduces new challenges and requires strong collaboration between the design firm, module integrator, and pipe spool fabricator, as well as other principles.
This article is written as a brief guide to highlight several areas where problems can arise in the design and construction of modular piping systems.
- Pipe hangers and their placement can result in significant pipe stress issues. Improperly located fixed points can prohibit the proper functioning of expansion loops. Additionally, weld beads can interfere with the desired sliding movement of pipes. The design firm and module integrator should take care to provision appropriate supports beyond the adoption of manufacturer-recommended spacing.
- Tolerance stacking can create issues when fabricating long mains. When building an 800-foot-long main from 25-foot-long pipe spools with +/- 1/8″ tolerances, one might find transitions to laterals that are 4″ off-nominal at the far end of the line. A module installation contractor might adjust for this gap with an ad hoc field-welded spool piece. However, a more optimal solution would be to provision for this allowance in the initial design rather than leaving it to the contractor’s discretion.
- Clearance in pipe racks can also be a challenge. This is particularly true with mains – industrial wastewater (IWW) drains, for example. It is not uncommon for initial designs to be impossible to load into racks, such as the large branches off the mains. This incompatibility is generally overlooked unless the system is initially designed around the racks. Before ordering pipe spools from a fabricator, it is recommended that the module integrator align the system model with their rack design. It may be necessary that they make adjustments to their rack design.
- Plastic pipe is relatively light and easy to lift into racks. In many cases, it is optimal to extend spool lengths to the maximum transportable size.
The issues outlined above can often be mitigated by bringing spool fabricators and module integrators into the design process as early as possible. Each role brings a suite of solutions and constraints that inform the optimal design. With strong collaboration between all principles, the full benefits of OSM can be realized for the customer.
EDITOR’S NOTICE: Please note, the information in this article is for educational purposes only and does not supersede any Asahi/America technical information or product specifications. Please consult Asahi/America’s technical department at 1-800-343-3618 or pipe@asahi-america.com on all product applications in regards to material selection based on the pressure, temperature, environmental factors, chemical, media, application, and more.