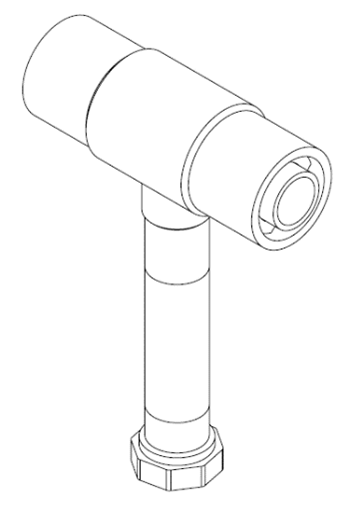
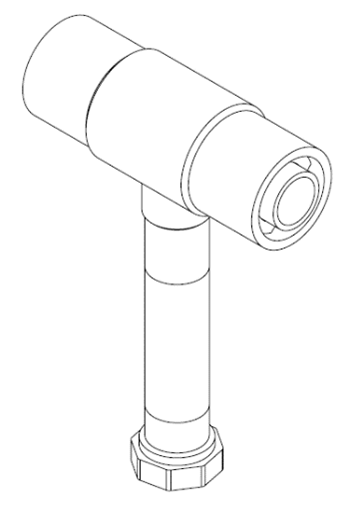
November 1, 2022
Inner Circle
Leak Detection: What Is It and Why Should It Be Used?
Contributed by Mark Gore, Business Development Manager
Leak detection in process piping can be a complicated part of any system, so why should it be used? The simple answer is that we are stewards of our environment and responsible for people’s safety. However, it has much more nuance than such a simple statement can capture, so here are some thoughts on the subject.
There are three types of leak detection systems. The first is visual detection (i.e., simply watching for leaks), which is used everywhere, from our homes to offices to production plants. It is also as straightforward as it sounds; you see a leak on a pipe and follow it to its source. While it may be simple, effective, and low cost, visual leak detection can’t always accurately pinpoint leaks, and it relies on human operation in most cases.
That’s where a method such as visual leak detection can turn dangerous. Say you encounter a cyanide or phosgene leak. Is that a chemical you would want to pinpoint the source of manually? Obviously not. Therefore, there are realistically two effective means to identify a leak and find its source; Low Point Leak Detection (LPLD) and Full Line Cable Leak Detection (FLCLD).
To utilize either of these two methods, a double containment piping system must be implemented. EPA Regulation 40 CFR 280 regulates Underground Storage Tanks (USTs) to minimize the effects of a leading source of groundwater contamination. All pressurized underground piping connections to USTs must be secondarily contained and have automatic line leak detection. The code defines secondary containment as “a release prevention and release detection system for a tank or piping” featuring “an inner and outer barrier with an interstitial space that is monitored for leaks.” These interstitial spaces are called sumps, where leak detection occurs in double-containment piping systems. Now, that’s a lot to consider when designing an underground piping system.
On top of those specifications, with the implementation of Superfund and CERCLA, the EPA has the power to hold parties liable for any waste, accident, spill, or release into the environment, which could make the worst of a bad situation when already dealing with harsh or aggressive chemicals.
Finally, the other governmental regulatory body involved with underground piping system safety is the Occupational Safety and Health Organization (OSHA) or the OSHA Safety Triangle. This regulation requires that after all other federal laws have been met with regard to secondary containment in piping systems, you must also ensure the protection of the personnel and the ecosystem from the dangers of exposure to aggressive and dangerous chemicals. In other words, federal regulations, EPA, and OSHA all jointly recommend using double containment piping systems and a leak detection system to protect the environment and those working in it.
Now that a double containment piping system has been settled upon and visual leak detection is out of the question, Low Point Leak Detection (LPLD) and Full Line Cable Leak Detection (FLCLD) are the options to choose from. So, what exactly are these systems, and how do they work?
Low Point Leak Detection (LPLD) is a system similar to manual leak detection but utilizes electronic sensors in place of manual valves or plugs and does not require human interaction to identify the leak in the pipe.
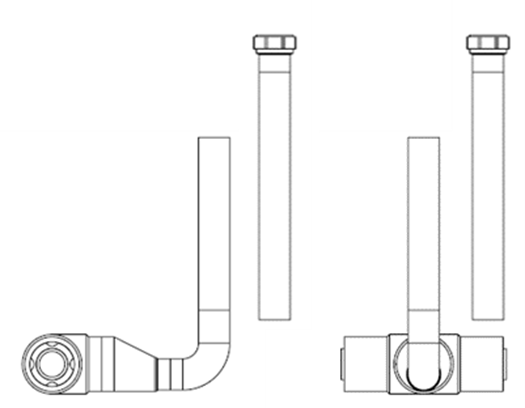
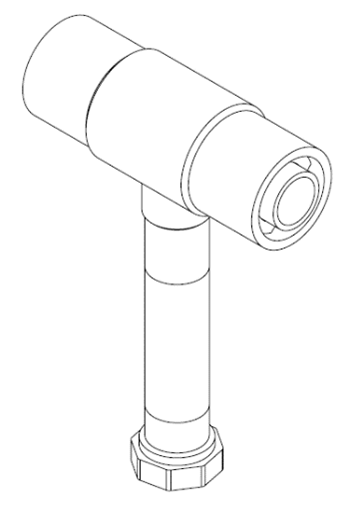
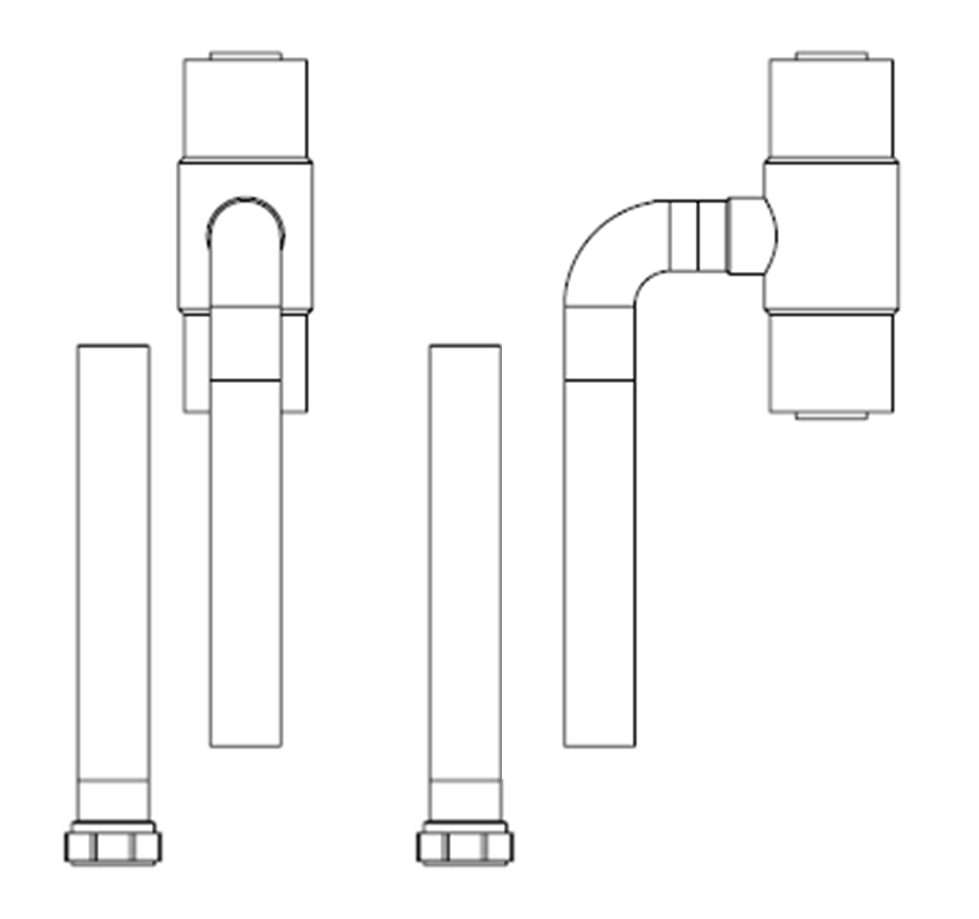
In the first drawing to the left, a conductivity probe or a float switch can be used to indicate that a leak has occurred and can then send a signal to a PLC or a light to produce a visual indication of a leak in progress. Conductivity probes are triggered via the detection of all conductive liquids: water, acid, bases, or chemicals. Float switches are designed to detect changes in the fluid, and if the float has been raised, the relay is activated. These two methods of detection are simple and cost-effective.
Why might we use one over the other? Conductivity probes are generally best in piping systems because they trip immediately upon contact with a liquid. Float switches are good for tank applications since they activate after reaching a certain volume level where the relay is activated. The LPLD system can be designed in multiple configurations: below ground with a low clearance, overhead design, or vertical design.
The final type of leak detection system is Full Line Cable Leak Detection (FLCLD), a system also known as Continuous Leak Detection Cable (CLDC). Continuous leak detection cable systems offer the most accurate method for detecting leaks in a double-contained piping system, as they can locate multiple leaks without loss of accuracy and sensitivity. With this system, a leak’s location can be pinpointed within five feet or less from the source by using time-domain reflectometry technology as the basis for searching, similar to radar. Thousands of pulses are sent out each minute to continually monitor the cable and create a map in its memory to compare to the current image of the piping system. When a leak occurs in sufficient quantities to make the cable “wet,” the cable will then alter its electrical properties, causing a difference in the current image and the system’s memory, thus pointing to the leak’s location. A signal is sent to notify the PLC operator that a leak has occurred within five feet of the approximate location. You could also use a cable that, when a conductive liquid comes in contact with it, the current changes the voltage of the circuit and triggers an alarm to be activated. In either method, full-line cable accuracy is achieved.
This system, however, is the costliest of the approaches discussed. The return on investment cycle is long due to the design engineering requirements based on system and component size, the number of access ports, the annular space required to pull the cable through the system, and the cable tie-ins at a central alarm location (PLC). With an FLCLD/CLDC system, the cost may be higher, but the accuracy and reliability of the system are enhanced to a degree where it can continually monitor the system.
So, why use leak detection in a double containment piping system? Again, the simple answer is we are stewards of the environment and responsible for people’s safety. However, that statement requires background knowledge of federal regulations, EPA regulations, and OSHA regulations and knowing what kind of system to use in the correct applications. Do you want to use manual/visual leak detection, upgrade to Low Point Leak Detection, or splurge on Full Line Cable Leak Detection for your system? The choice is yours.
EDITOR’S NOTICE: Please note, the information in this article is for educational purposes only and does not supersede any Asahi/America technical information or product specifications. Please consult Asahi/America’s technical department at 1-800-343-3618 or pipe@asahi-america.com on all product applications in regards to material selection based on the pressure, temperature, environmental factors, chemical, media, application, and more.