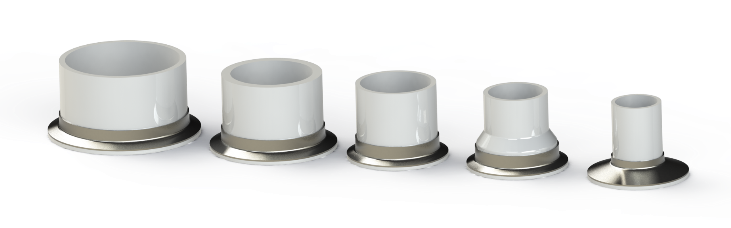
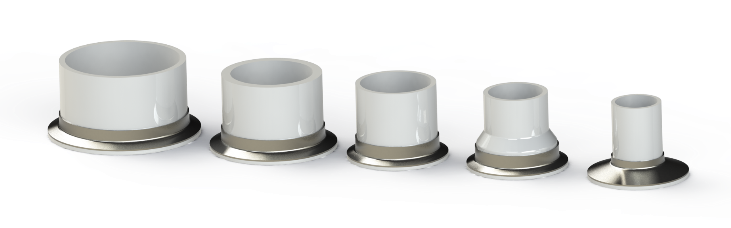
August 1, 2022
Inner Circle
Comparison of Thermoplastics and Stainless Steel for the Biopharmaceutical Industry
Contributed by Pat Higgins, Business Development Manager
High purity water is used extensively in manufacturing pharmaceutical and biotech medicines. Piping material for generating and transporting high purity water includes stainless steel and thermoplastics, such as polyvinylidene fluoride (PVDF) and polypropylene (PP).
The use of thermoplastics in high purity water systems for pharmaceutical and biotech offers many advantages over stainless steel systems. It is essential to understand the material properties of thermoplastics when evaluating their suitability for your system requirements. Considerations such as thermal expansion, operating pressure, and system temperature must be considered when choosing a system to match the process. If a water system’s requirements falls within the acceptable range of the thermoplastic operating conditions, the choice of plastics over metals can provide many benefits, including years of trouble-free and low-maintenance operation. This is demonstrated and proven by the many existing PVDF and PP purified water and water for injection (WFI) systems.
Advantages of thermoplastic high purity water systems over stainless steel systems include:
- Corrosion- and Passivation-Free: Corrosion or rouging is common in metal systems, but is not an issue with thermoplastics. Plastics do not corrode; by eliminating rouging, you also eliminate the many time-consuming and costly operations associated with it. Passivation, for example, ceases to be required.
- Simplified Welding Techniques: Thermoplastic systems are joined by various thermal-fusion welding techniques. PVDF and PP resins are extremely pure and consistent from lot to lot. This purity and consistency enable repeatable and reliable welding techniques. Stainless steel welding concerns, such as sulfur concentration, chromium depletion, and the condition of tungsten electrodes are not issues in thermoplastics. The result is simplified welding and installation practices with thermoplastic systems.
- Superior Surface Finish: In high purity water systems, bacteria growth and biofilm are concerns that need to be minimized or eliminated. Surface finish is a critical factor in the proliferation of bacteria colonies. Rougher surface finishes can allow bacteria to adhere to the surface and resist flushing. High purity PVDF systems typically offer better surface finishes than stainless steel systems and better resistance to bacteria or biofilm growth.
- Purity of Material: The high purity grades of PVDF and PP have extremely low levels of extractability and provide superior purity compared to stainless steel. Metal ion contamination from stainless steel systems is a concern in some applications, especially biotech.
- Reduced Operating Cost: Using plastics in a properly designed purified water system will save installation, operation, and maintenance costs. Cleaner operation and removal of passivation requirements result in sanitation cost savings and reduced need or elimination of system shutdowns.
Joining methods for thermoplastics in biopharmaceutical applications include welded connections as well as the use of sanitary adapters. Asahi/America recommends infrared (IR) or beadless welding for high purity biopharma water systems. IR minimizes weld bead size to help prevent biofilm growth and contamination of the weld zone. Beadless welding is commonly used in the life science and pharmaceutical industry, where the prevention of bacteria growth is a crucial requirement. With no weld bead or crevice in the joint, it eliminates a potential location for bacteria and biofilm buildup inside the piping system. Asahi/America’s SP 110-B beadless tool welds pipe, valves, and fittings from 1/2″ – 4″ in diameter. The tool uses an encased heater and pressurized balloon to eliminate the weld bead. Like the rest of Asahi/America’s SP tool series, the welding process is largely automated to produce consistent and repeatable welds. The large size range of the tool allows users to work without the need for multiple devices on a project. The completely automated fusion process provides unmatched welding reliability, ease of use, and short weld times. An automated planing depth feature enhances fabrication capabilities, while the magnetic clamp inserts allow for a quick pipe size change. An internal validation program provides several QA sources, including multiple label printouts, copy label printouts, stored electronic data, and a PC download program.
A video highlighting the operation of the SP 110-B beadless welding tool in the above photo is available here.
Another standard option for joining plastics in biopharma applications is the use of tri-clamps, or sanitary adapters.
High purity sanitary adapters are commonly used in many pharmaceutical and life science applications and are held together with hygienic clamps (sanitary clamps) and a gasket to ensure a smooth seal. These mechanical connections help make routine work such as cleaning and sterilization quick and easy. Sanitary adapters are critical in providing a sterile environment for application processes. Poor sanitary adapter installations can compromise a process’s integrity, resulting in cross-contamination, loss of batch, possible injury to workers, and bacteria infestations. Improper connections risk an opportunity for bacteria to grow in crevices or cause leakage between the connections. Working personnel who interact with these systems must know the importance of having the correct parts, tools, and training to connect and disconnect piping systems without issue.
Asahi/America offers a High Purity Piping Sanitary Adapter & Hygienic Clamp Connections Best Practices Guide, which provides thorough instructions and answers common questions about proper material selection and installation of Asahi/America’s high purity sanitary adapters.
Asahi is also developing a family of sanitary adapters with stainless steel backing set to be released at the end of 2022. Stay connected for news and updates by clicking on our social media network below.
EDITOR’S NOTICE: Please note, the information in this article is for educational purposes only and does not supersede any Asahi/America technical information or product specifications. Please consult Asahi/America’s technical department at 1-800-343-3618 or pipe@asahi-america.com on all product applications in regards to material selection based on the pressure, temperature, environmental factors, chemical, media, application, and more.