November 14, 2024
Duo-Pro® / Double Containment for Drainage Applications in Pharmaceutical Installations
Contributed by Pat Higgins, Business Development Manager (Life Sciences, Food & Beverage, and Lab)
In 1988, the Environmental Protection Agency (EPA) directed that underground transport of hazardous materials be protected from release into the environment in its Standard 40 CFR, Part 280 & 281. To comply, transport systems must:
- Have manual leak detection, at the very least, for drainage systems;
- Have automated leak detection for pressurized systems;
- Be double contained;
- Have outer containment that can retain media transport for a minimum of 30 days.
EPA Regulation 40 Code of Federal Regulations (CFR) 280 lists more than 800 hazardous chemicals that must be double contained. According to the EPA, chemicals used in pharmaceutical manufacturing that are considered hazardous include arsenic, barium, cadmium, chloroform, chromium, lindane, mercury, and selenium, among others. Double contained piping systems protect the environment and prevent the need for costly cleanup and project delays should there be a leak in the inner/carrier pipe.
Many companies have safety policies calling for double containment in both underground and overhead piping systems. OSHA maintains a list of hazardous chemicals and permissible exposure limits. They recommend isolating/enclosing a process to control the exposure of personnel to toxic substances.
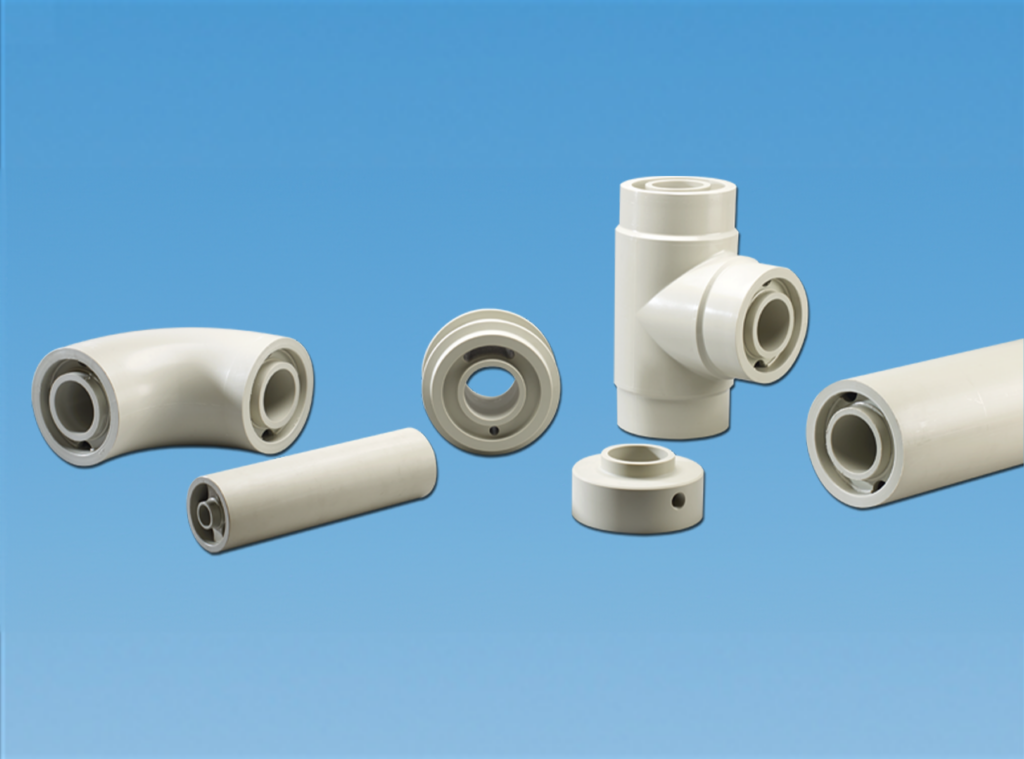
Asahi/America’s Duo-Pro® double containment piping system has been specifically engineered to exceed the EPA’s piping system requirements. A common use of the Duo-Pro® system is for wastewater drainage systems at pharmaceutical plants. Duo-Pro® has a full complement of fittings for drainage applications. Its excellent resistance to chemicals, wide range of high-temperature applications, and easy installation are just some of the advantages of the Duo-Pro® system. Dual containment piping protects against the remote chance of a leak in the carrier pipe transporting the media.
In addition to below-grade systems, many companies have adopted policies to use double containment for overhead piping to protect personnel from a possible leak of a harmful chemical.
The majority of double containment systems installed worldwide are thermoplastic due to the ease of joining and the resistance to hazardous chemical media and underground moisture. Duo-Pro® offers highly corrosion-resistant materials such as polypropylene, PVDF, and ECTFE. Standard pipe diameter sizes are 1″ x 3″ through 16″ x 20″. The system provides maximum versatility to meet the unique requirements of each application. In a dual containment piping system, the internal pipe is referred to as the carrier pipe, and the external pipe is the containment pipe. Duo-Pro® offers mix-and-match options, allowing system designers to specify different pipe materials and pressure ratings for the carrier and containment pipe based on media and pressure changes throughout an entire system. In most cases, a system will use the same material for both the carrier and containment pipe, but some systems implement a combination like PVDF carrier pipe inside polypropylene containment pipe as a cost-saving measure.
The selection of material type for the carrier pipe is based on common piping practices using variables such as what chemical(s) will be in contact with the pipe and the chemical concentration. Other considerations include system operating temperature, pressure, and flow rate of the media. Once the carrier pipe has been selected, the containment pipe must be chosen. The sizing of the containment pipe for underground systems requires consideration of static soil load and dynamic traffic load, leak detection requirements, and operating pressure. For Duo-Pro® systems, there are several leak detection methods to choose from, including manual leak detection, electronic low-point sensors, and continuous cable leak detection.
Manual Leak Detection
The EPA requires at least a manual leak detection system for drainage systems, although other methods can be used, such as low-point sensor or continuous cable. Manual leak detection is the simplest of the three methods. It is accomplished by accessing the annular space, generally at low points in a system, with a valve, plug, or pipe riser in order to grade. The EPA mandates periodic manual inspection of the ports at least every 30 days.
Electronic Low-Point Leak Detection
Low-point leak detection is similar to manual leak detection but utilizes electronic sensors tied in at a central alarm location instead of manual valves or plugs. This automated detection process for buried applications locates leaks within a zone or sector of a system. A wide variety of low-point sensors are available with varying functionality, and the selection of sensor type is often dependent upon the transported media. The two most common low-point sensors are conductivity probes and float switch adapters.
Continuous Leak Detection Cable
Continuous leak detection is more expensive than manual or low-point but offers the most accurate method of automated leak detection. The leak detection cable is installed in the annular space between the inner and outer pipe. Sensor cable systems are capable of locating multiple leaks without loss of accuracy and sensitivity. Leak locations can be narrowed to within five feet of the source. Sensor cables utilize time domain reflectometry technology as the basis of their leak detection method, which operates similarly to radar. Thousands of times each minute, safe energy pulses are sent out on the sensor cables. As these energy pulses travel down the cable, reflections are returned to the monitoring unit, and a map of the reflected energy from the cable is stored in memory. The presence of liquids on the sensor cable, in sufficient quantities to “wet” the cable, will alter its electrical properties. This alteration will cause a change in the reflection at that location, which is, in turn, used to determine the location of a leak.
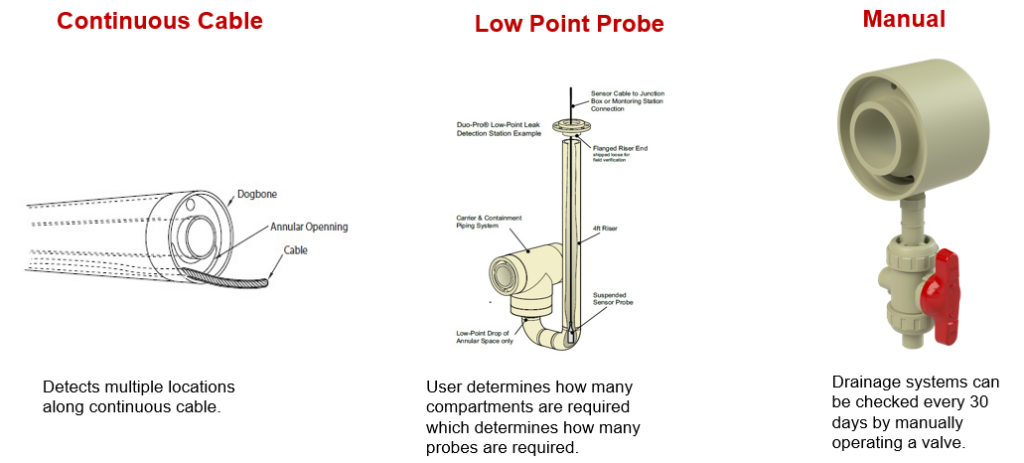
Welding Methods
Like single wall piping, Duo-Pro® double containment systems utilize butt fusion assembly. Butt fusion is reliable and is well-suited for double wall systems; by properly aligning the carrier and containment piping with the support disc, both inner and outer pipe can be welded simultaneously. This reduces assembly time and the need for extra fittings such as couplings. What can be accomplished in one weld can take up to four welds in other systems, which require welding the inner and outer pipes separately on either side of a coupling. When building a system of dissimilar materials (for example, one with a PVDF carrier and PP containment pipe), the pipes cannot be welded simultaneously due to different heat and joining force requirements. For these systems, staggered welding is required, where the inner pipe is welded first, and the outer pipe is welded second using a special annular heating element. Staggered fusion takes more time due to the extra welds, but this method may still prove economical when compared to simultaneous butt welding in systems that use similar materials for both pipes, such as PVDF for both the carrier and containment.
Thermal Expansion
As temperatures rise and fall, thermoplastic materials expand and contract to relieve stress. Stress analysis can be performed to calculate the amount of flexibility a system will require. The methods used to handle expansion in double containment piping systems are similar to those used in single wall piping systems. A flexible design system uses a fitting that anchors both the carrier pipe and containment pipe while allowing the carrier pipe to move in the containment line. As a note, the containment area may need to be expanded to address thermal expansion and contraction of the carrier pipe. For a restraint design, proper use of restraint fittings (such as dogbones®) and guides throughout the system will isolate the fittings from thermal stress and end loads when temperatures fluctuate.
Asahi/America has been providing double containment piping systems to meet Environmental Protection Agency (EPA) standards for over 25 years. As the innovator and patent holder of many double containment specialty devices, Asahi/America is equipped to help engineers and designers fabricate and install double containment piping systems with confidence.