

May 1, 2021
Inner Circle
High Purity Piping Systems: Material Selection and Welding
Contributed by Dave Stiles, Business Development Manager, High Purity Products
In both semiconductor manufacturing and the life science industry, purified water (PW), deionized water (DI) and ultrapurified water (UPW) play critical roles in final product quality. The specification of appropriate pipe materials and joining methods is an important consideration for MEP system engineers. Specifying engineers in these disciplines already have a knowledgeable understanding of material selection, but did you know that joining methods may have a bigger impact on system performance? A specifier must strike a balance between reliability, performance, regulatory compliance and economics. Let’s take a look at joining methods, typical applications, and limitations of those methods.
Typically, the design process begins with a review of the end-users water quality requirements. The list of established standards is large. Each has been developed to suit a given application. Some put the greatest emphasis on resistivity, while others prioritize total organic carbon (TOC), particles or bacterial loads. Fortunately, these standards can be broken down into three broad groups that align with Asahi/America’s high purity pipe systems (see table 1). While there is some degree of flexibility, a specifier should take care to consider the available valves, pipe sizes and pressure ranges that can constrain the selection.
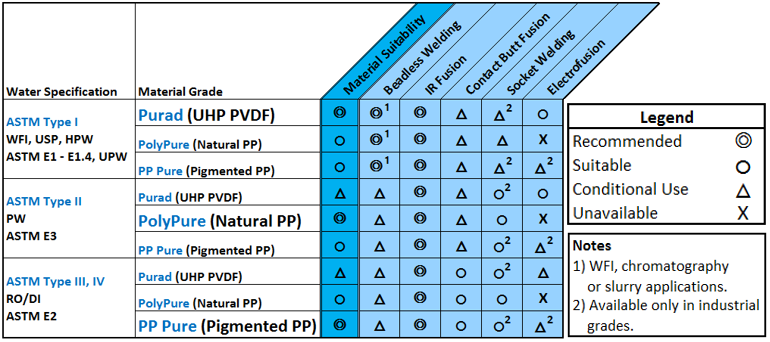
After defining a suitable material grade, the question of welding methods must be addressed. Inappropriate welding or mechanical joints can severely degrade a system. Infrared (IR) fusion stands out as having excellent performance due to its’ small bead size and repeatability. This stems from using force-control technology that employs a pressure transducer, worm drive and preprogrammed parameters. The pressure transducer limits the joining force and prevents too much molten material from being driven out of the heat effected zone, causing a cold weld. This method is in contrast with distance-control technology found in many older tools. Additionally, the non-contact heating method does not introduce contaminants into the bead. In most high purity applications, IR fusion proves to be an optimal solution. However, to any rule, there are exceptions.
Notably, beadless welding, which uses a specially designed balloon inside the piping during the welding process to eliminate any bead, may be preferred for systems that need to be fully drainable or are particularly sensitive to biofilm growth such as water for injection (WFI) or chromatography. When opting for beadless it should be understood that it is the slowest welding method and is relatively expensive. The installer is re-melting the thermoplastic and forming one homogenous material. With automated welding equipment, beadless welding is quite reliable, but can be daunting for contractors unfamiliar with the process. Beadless welding takes planning because the internal balloon must be removed after the weld. This is covered in Asahi/America’s training procedures prior to job startup. As with all welding methods, it is critical that the fabricators receive manufacturer training that meets all current standards and codes prior to completing any work on a project. Asahi’s certification program typically consists of training the operators to use the equipment and ensuring they are capable of producing reliable welds.
Socket welding is a very simple method of joining using a heater bushing and coupling, which fuses the pipe together. This method shows merit in less critical applications or small jobs where the cost of operating an IR welding tool is prohibitive. Socket welding results in large internal beads and crevices that may support biofilm growth. If the application is not bio/pharm requiring full drainage, consider allowing socket welding for a certain percentage of welds. This flexibility provides contractors the ability to utilize this method along with IR fusion for difficult locations such as final tie-ins or otherwise impossible joints.
Contact butt fusion is another viable option for some applications. The internal bead is larger than IR welding, but smaller than socket welding. The process is less sensitive to air circulation than IR welding and can therefore be done in a wide variety of fabrication environments. Unfortunately, it can also introduce some level of contamination into the bead. This welding method is most common for chemical applications, double containment or industrial use.
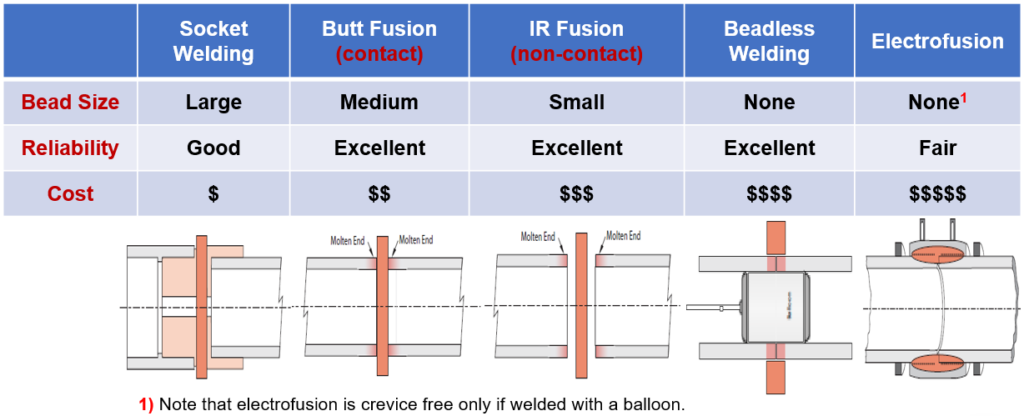
Electrofusion is a joining method that uses the heat gained from resistance of an electrical coil when power is applied. The coil for Asahi/America’s materials is always embedded within the coupling to prevent exposure to the system fluid. This technique has only a limited role in high purity systems and is generally only recommended when no other option is available. It’s excellent for difficult to reach tie-ins, but will leave a small crevice between pipe ends. This crevice may harbor biofilm and should therefore be avoided in applications that demand low TOC. The couplings for polypropylene systems are technically industrial grade. Their availability is mentioned for informational purposes only and not a recommendation they be used in high purity applications. However, in the case of half-inch to two-inch PVDF, Asahi/America offers a unique system that uses a balloon inserted into the ID of the pipe. The high purity balloon is inflated during fusion, which presses against the inner wall preventing the formation of a crevice.
Most contractors own welding equipment and employ people who have received special certifications from the American Welding Society (AWS) to perform thermoplastic welding. For those without their own welding equipment, Asahi/America maintains a fleet of fusion equipment. It is important to specify who can weld piping for applications. Asahi’s certification process ensures that fabricators receive sufficient training to operate equipment and reliably perform welds. For further inquiry, Asahi/America can provide a comprehensive engineering design guide and product specifications, as well as lunch and learn opportunities for your team. Feel free to reach out to the Asahi BDM team with any questions.
EDITOR’S NOTICE: Please note, the information in this article is for educational purposes only and does not supersede any Asahi/America technical information or product specifications. Please consult Asahi/America’s technical department at 1-800-343-3618 or [email protected] on all product applications in regards to material selection based on the pressure, temperature, environmental factors, chemical, media, application, and more.