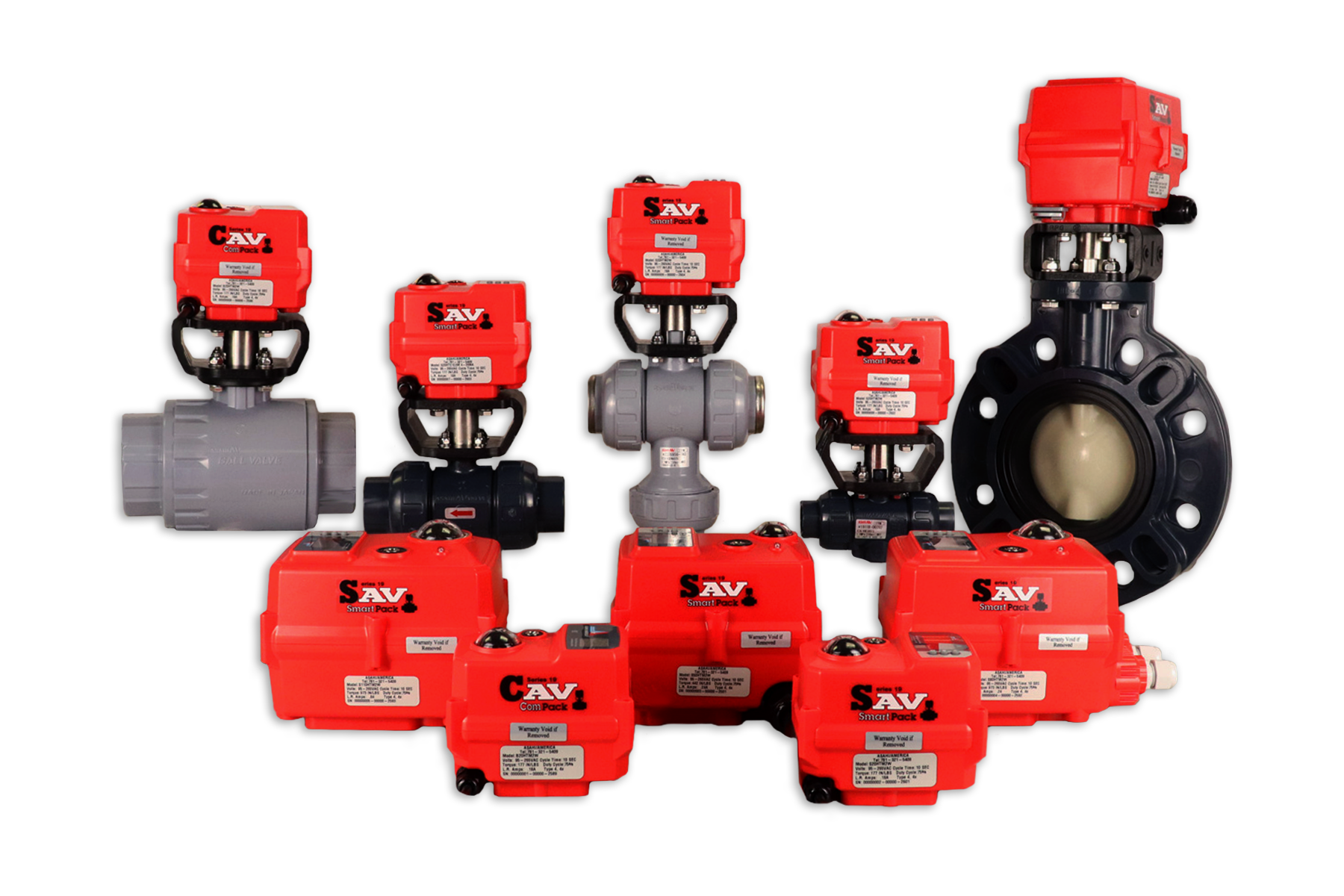
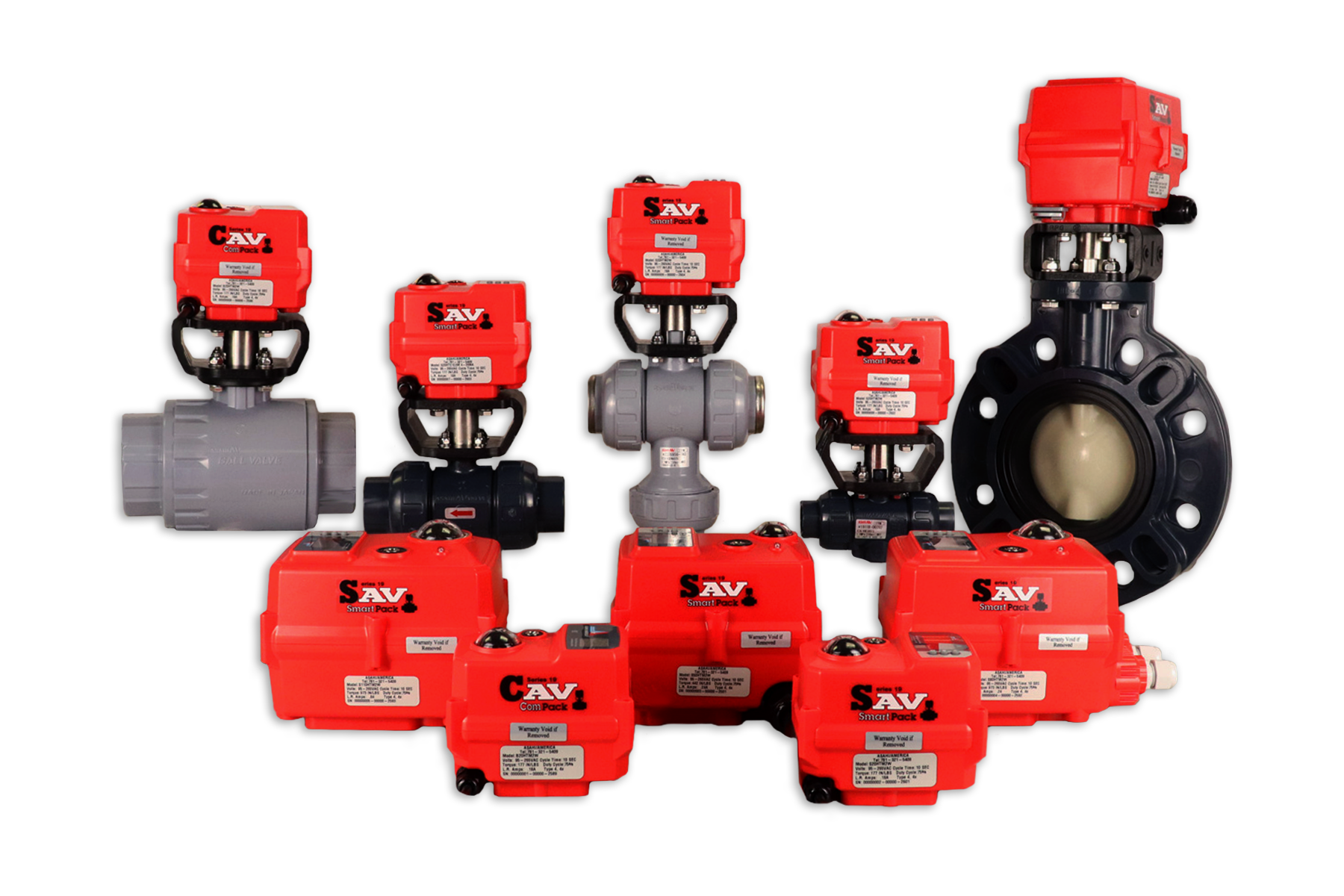
September 1, 2021
Inner Circle
Choosing an Actuator: Factors and Considerations
Contributed by Shane McDaniel, Business Development Manager, Valve and Actuation Products
While typically the most common and thoroughly discussed component of any process system is the valve, one component that is equally critical, yet often misunderstood, and sometimes even overlooked is the actuator. Whether it’s a simple manual valve, severe service flow control valve, or critical on/off isolation valve, engineers and suppliers spend hours discussing, specifying and designing valve packages that can withstand a multitude of factors for operation. Similarly, there are a variety of factors engineers and specifiers must consider when choosing an actuation production to automate these valves.
Below is a non-exhaustive list that reviews some of these important considerations:
- Application
- Control System Scheme
- Asset Reliability and Criticality
- Cost
Application – What are we trying to accomplish in the system with this valve? Is this a flow control loop, an isolation valve, or pump protection? What are the factors in the process such as pressure, temperature, and flow rates required for the application? While these questions are typically considered when specifying a valve, it is still critical to understand how they can impact the performance of an actuator. For example, if an actuator is undersized, which is not specified correctly to the valve and process variables, it may not have the proper amount of force to fully close the valve, resulting in unreliable process control.
Control System Scheme – How will the control system interact with the actuator? Will the actuator utilize air or electricity to operate? Will there be a control signal in the form of a relay output and solenoid, or 4-20mA signal to a controller? What feedback requirements are required from the actuator? For example, a feedback signal in the form of 0-10 volts to verify valve position back to the PLC.
Asset Reliability and Criticality – Another negative result of choosing the wrong actuator is the loss of repeatability in control. The wrong actuator can work in an application for a short time, but if this valve did not turn as a result of system malfunction, what impact would that have to the process; to the employees; or to the environment? What action does the unit need to take in the event of loss of control or power? Understanding how the valve, actuator and any controls work together are critical to success. Furthermore, are there legal requirements, codes, or standards that demand a specific level or performance? The regulations and certifications vary across industries and applications.
Cost – While this is not the only deciding factor, every engineer must consider the overall project budget when making their actuator selection. While there is the consideration of the initial investment cost, there is the also the need to operate and maintain an asset over its lifecycle. Depending on the air or electric consumption, and cost to maintain and repair, a lower initial cost benefit may be lost over time when trying to resolve issues with a “trouble unit”.
Every actuator has to perform, at minimum, the following functional purposes:
- Actuators process the control input to move the valve closing member – whether ball, disc, or plug – to a desired travel location; they must be able to hold the closure member in that position reliably until the control signal changes. In a pneumatic actuator, this is achieved with applying air to a diaphragm or piston in order to move the valve. Pneumatic positioners and electro-pneumatic positioners are common ways to convert small pneumatic or electronic signals for modulating service. An electric actuator receives a control signal of a change in voltage, current, or resistance and responds by utilizing an electric motor and gear train to convert rotational force into torque or thrust.
- When fully closing or opening a shutoff valve, actuators must have the torque or thrust available to provide the desired shutoff, and breakout torque available to move the closure member out of the seat. In pneumatic actuators, the amount of torque is dependent on the size of the surface receiving the supply air, such as a piston, and the pressure applied, typically measured in psi. Electric actuators utilize motor size and gear ratio to achieve toque and speed outputs.
- Actuators should operate the valve at a speed necessary to achieve optimal results for the process, while reducing mechanical wear and ensuring the longest possible lifecycle for the package. Applying a large amount of force, in a rapid manner and repeatedly, will lead to damage of both the valve and actuator if not specified correctly. In a pneumatic application, it may be necessary to increase the size of the actuator to ensure more power is available, or specialized control accessories such as positioners, solenoids, boosters, or quick-exhaust may be employed to increase cycle times. The speed of an electric actuator can be manipulated in a few ways. Some actuators have electronic boards that manipulate the speed output, while still maintaining constant torque. Other actuators have to be assembled with the appropriate gear ratio and motor configurations, limiting this adjustment to purely mechanical.
- Actuators should have some level of failsafe – whether fail closed, fail open, or fail in position – and be able to maintain that position until normal process operation can resume. In a pneumatic system, this requirement has varying levels of complexity, which depends on the failsafe requirement. The most common option is a spring return unit that forces the actuator open or closed upon loss of supply air or control signal. This is the most common and most widely used in industrial applications. At times, it may be required to add extra accessories such as an accumulator tank, specialized solenoids and pneumatic relays to provide air to units without a spring, or meet fail in position requirements. In an electric actuator, battery, or capacitor, failsafes are quite common solutions. A battery, bank, or capacitor store energy and provide the energy as needed when power or control signal is lost. The mechanical tension of the motor and gear train then holds the valve in place until power is restored.
Looking at the variety of actuator technologies and control options available to select the right package can seem like a daunting task. At Asahi/America, we are ready and willing to help with whatever questions you have.
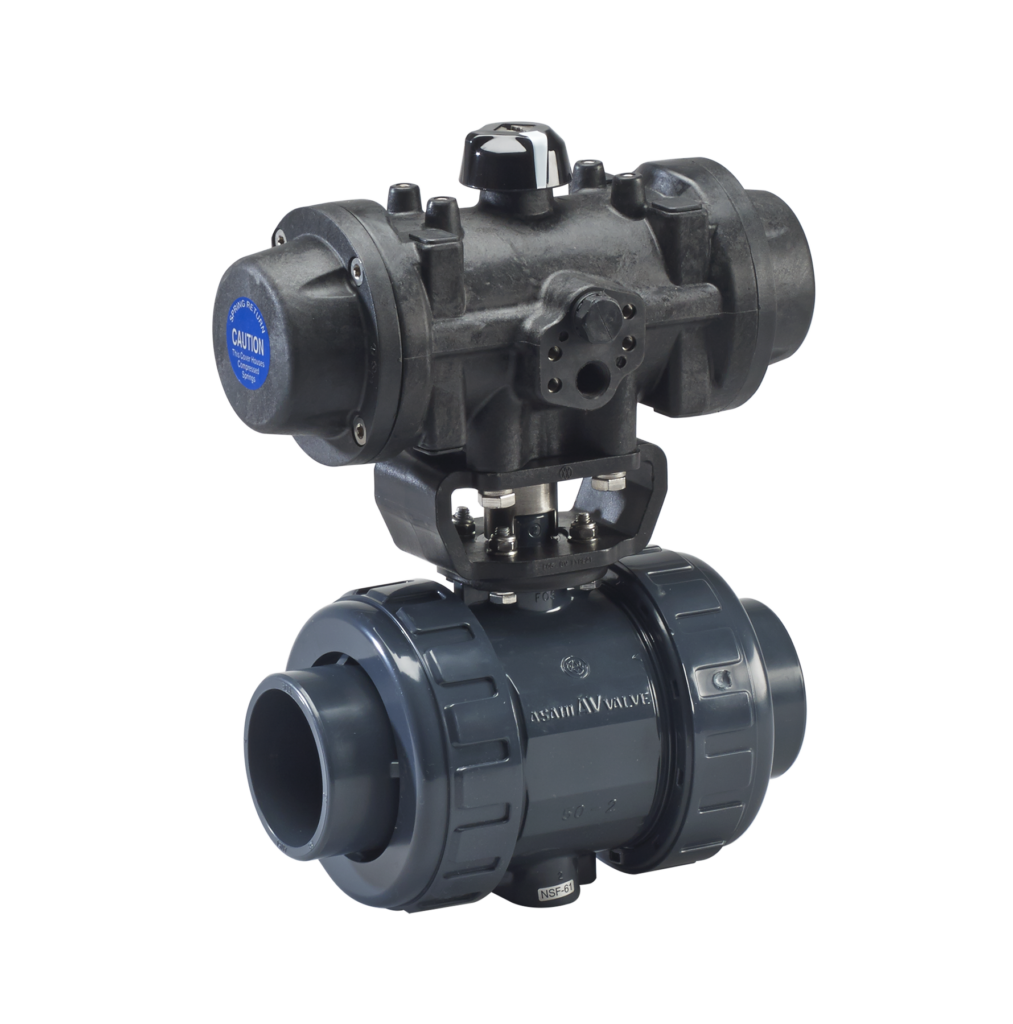
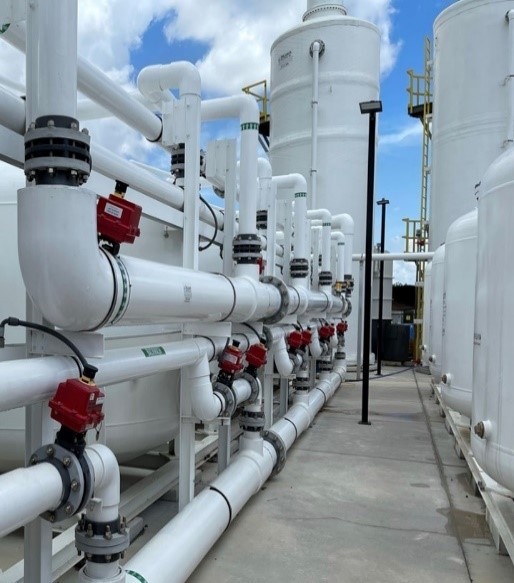
Asahi/America’s actuation products have dominated in industries such as chemical processing, water treatment, aquariums, pools, and semiconductor segments. Our core offering includes our well-tested and industry-proven Series 79 pneumatic actuator, along with controls and accessories to meet the need of any pneumatic application.
Asahi/America has an impressive range of actuation products that pair seamlessly with our thermoplastic valves, however, our experience doesn’t end there. Our Series 92 electric actuator has seen the same success in the aforementioned industries, and in the oilfield and other metallic valve applications.
Engineers are looking for suppliers to provide technologies and equipment that not only serve the basic purpose of process control in their facilities, but also suppliers who provide more features and benefits that maximize productivity, increase results, and solve problems that contribute to lost uptime and profitability.
Asahi/America has recently introduced the Series 19 electric actuator that will help bridge that gap for our customers and help guide them to the next level of actuation reliability and success.
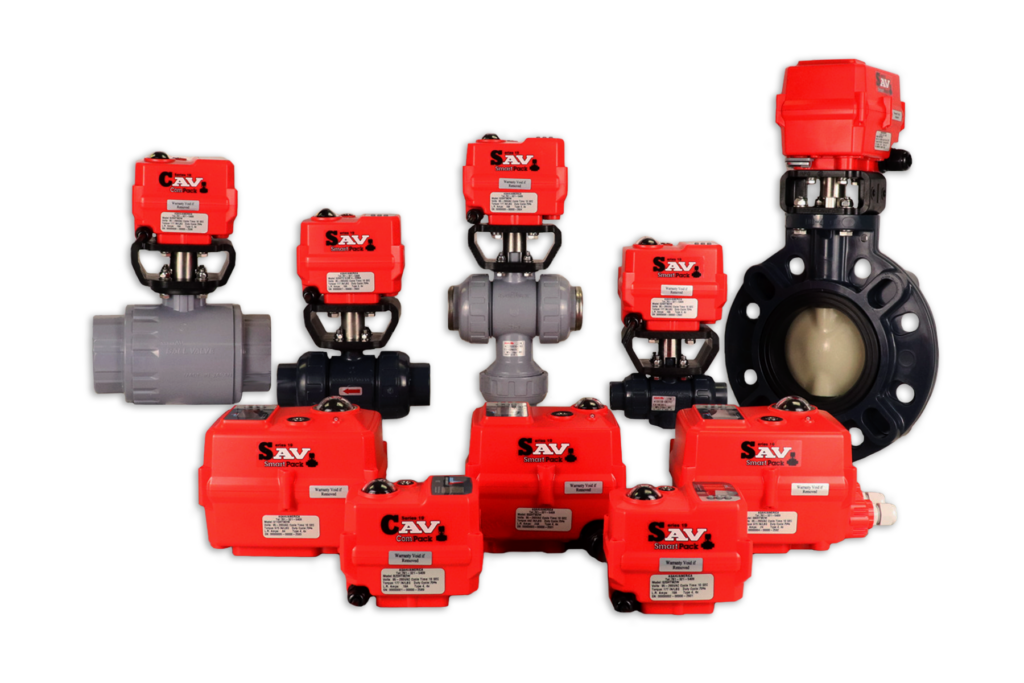
The Series 19 features intelligent firmware-driven design, compact footprint, and factory-engineered packages, such as the Series 19 and Type-21a SST flow control ball valve. Our users can count on accurate, reliable, and repeatable control for their applications.
Have a new application that you are not quite sure what to do next? Have an application that has been performing below expectations? Contact us today.
EDITOR’S NOTICE: Please note, the information in this article is for educational purposes only and does not supersede any Asahi/America technical information or product specifications. Please consult Asahi/America’s technical department at 1-800-343-3618 or [email protected] on all product applications in regards to material selection based on the pressure, temperature, environmental factors, chemical, media, application, and more.