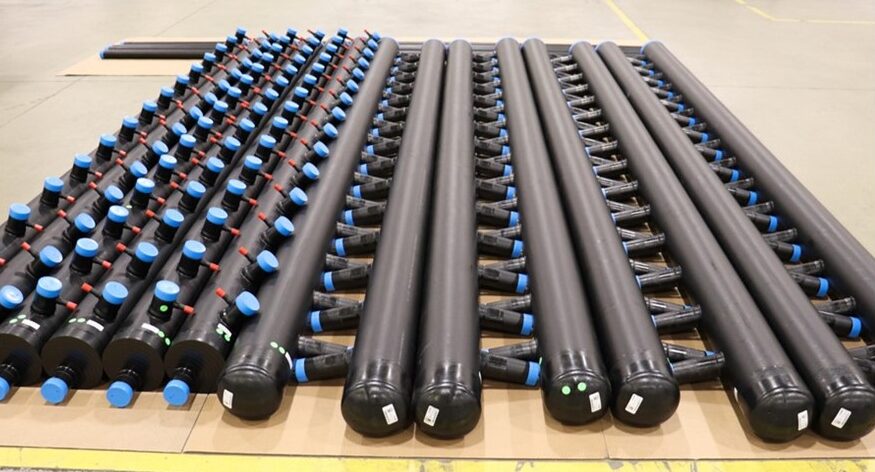
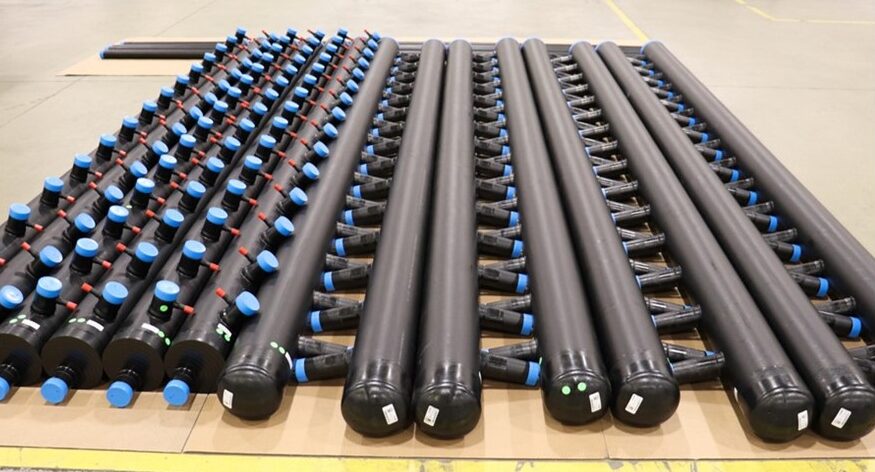
February 1, 2022
Inner Circle
Prefabrication: Increase Quality and Reduce On-Site Costs
Contributed by Pete Quinn, Business Development Manager, Fabricated Products
Asahi/America frequently fabricates spools and assemblies out of our engineered thermoplastic pipes to meet our customers’ dimensions, specifications, and delivery needs. We’ve been fabricating double containment systems since before we received our first fabrication patent in the late ’80s. Asahi continues to expand our capabilities and capacity through new equipment and personnel. We fabricate multiple types of high-density polyethylene (HDPE) pipe geared toward the water filtration industry that support skid builders with higher quality, longer-lasting filtration headers. We also focus on complicated assemblies to support large prefabricated projects that can ship directly to the job site, thus reducing field welds while drastically increasing cost savings for our customers.
No scope is too big or too small. Our fabrication process puts your needs at the center of attention and we can hold tight tolerances of 1/32” and 2 degrees angularity.
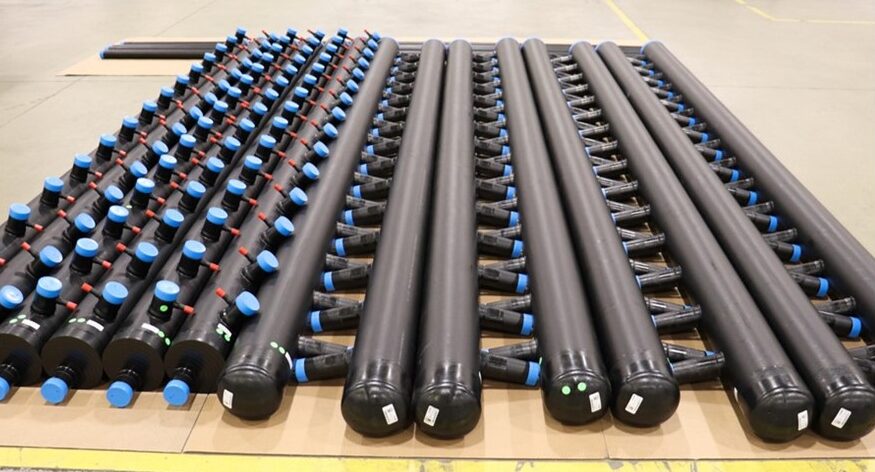
For customers who coordinate multiple trades and tight schedules, prefabrication may solve some logistics issues. The amount of time contractors can spend working on-site is limited by the congestion in work zones and onsite scheduling conflicts and various meetings that are scheduled throughout the day. Prefabricated products reduce costs by reducing the number of field welds and field construction.
If offsite fabrication isn’t already enticing enough, the added benefit of specific know-how and extra components helps eliminate the contractor’s need to order additional parts, in the event that dimensions are off or rework is needed on a pipeline spool. We are agile and responsive, if design changes are made during fabrications, we have plenty of inventory to redo the fabrication with minimal downtime and without jeopardizing the completion date.
Our automated manifold machine logs all welding parameters; logs are submitted to the customer before shipping. All welds are visually inspected and any anomalies are corrected. Although it’s an option, pressure testing is not necessary because the welding parameters are designed, tested, and automated. In the unlikely event that there is a leak in the field, we will repair or replace the fabrication.
To meet dimensional requirements, our Lawrence, MA location has a controlled environment where all fusion welds are done at 68° F. This helps with expansion and contractions issues where temperatures can fluctuate day by day or even within the same day. We also have cleanroom fabrication areas where we manufacture for the high purity industry.
Ensuring the fabricated parts get to their destination free from damage is no longer a concern when you consider our impressive crating and packaging options, which we highly recommend. We recently shipped out manifolds and spool fabrications to a water OEM project that was assembled in California (picture below). The crates were 40’ x 4’ and were lined with Styrofoam sheets. All the fabrications were locked in place to prevent movement on the cross-country delivery.
Asahi’s manufacturing expertise and dedication to our customers helped developed many long-term OEM partners that we have supported over the past few decades. Asahi dedicates manufacturing floor space to our OEM partners to ensure their ever-changing schedules and needs will be met. We are here to support your growing needs. Our capabilities include manifolds on automated equipment up to 12” diameter and with other equipment up to 24” diameter. Want to explore manifold opportunities with us? Contact Asahi/America today.
EDITOR’S NOTICE: Please note, the information in this article is for educational purposes only and does not supersede any Asahi/America technical information or product specifications. Please consult Asahi/America’s technical department at 1-800-343-3618 or [email protected] on all product applications in regards to material selection based on the pressure, temperature, environmental factors, chemical, media, application, and more.