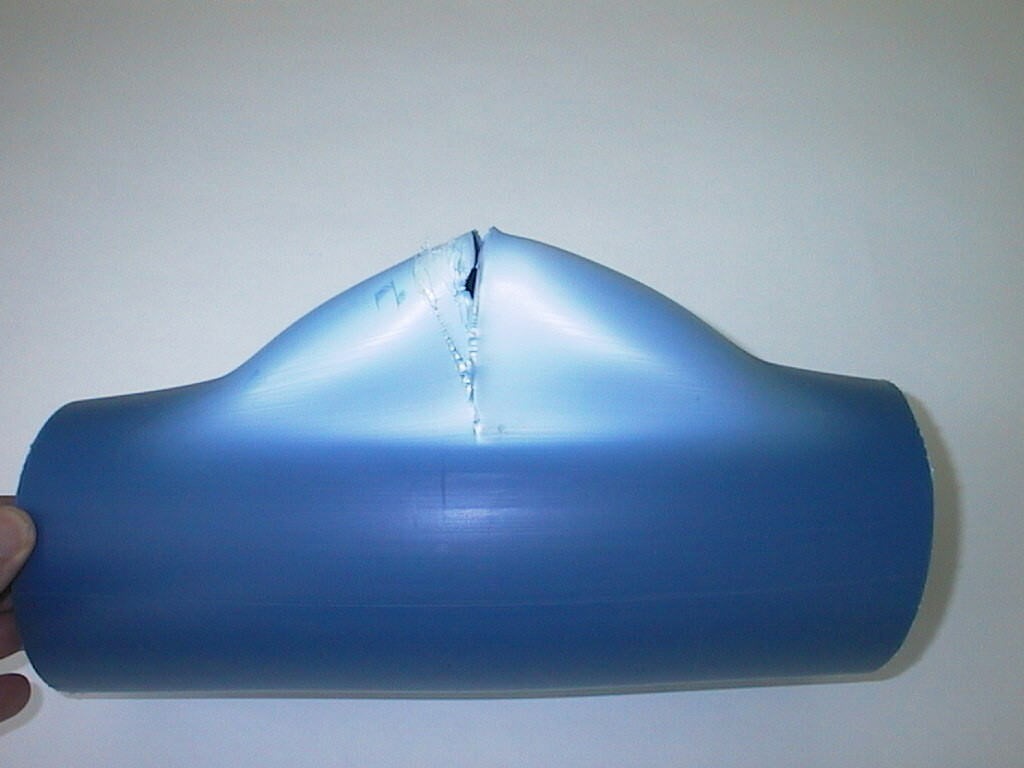
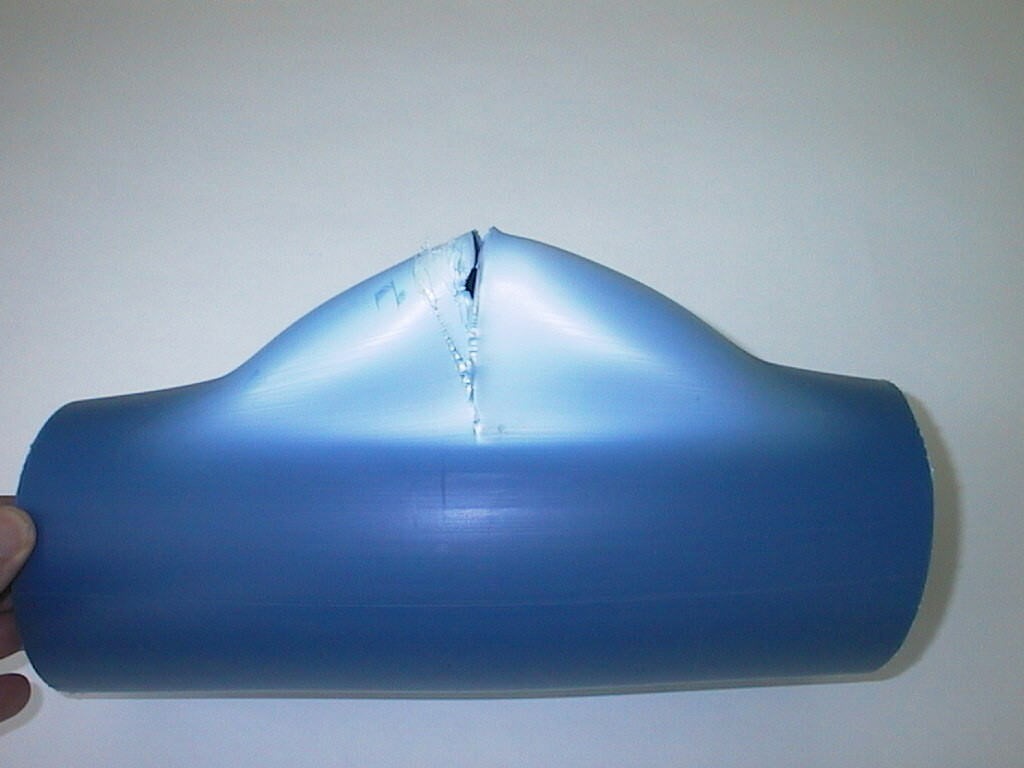
May 1, 2022
Inner Circle
Thermoplastic Pipes for Compressed Air – There is a Safe Option
Contributed by Rob Marsiglia, Industrial Piping Products Team Leader
There are limited, acceptable thermoplastic pipe options for compressed air because of safety concerns, high costs, and unsuitable application conditions. OSHA’s issued standards state that if thermoplastic piping materials are to be used for compressed air or gas applications, “the pipes must either be constructed of or encased in, shatter-resistant material” (OSHA standard interpretation dated February 28, 1991).
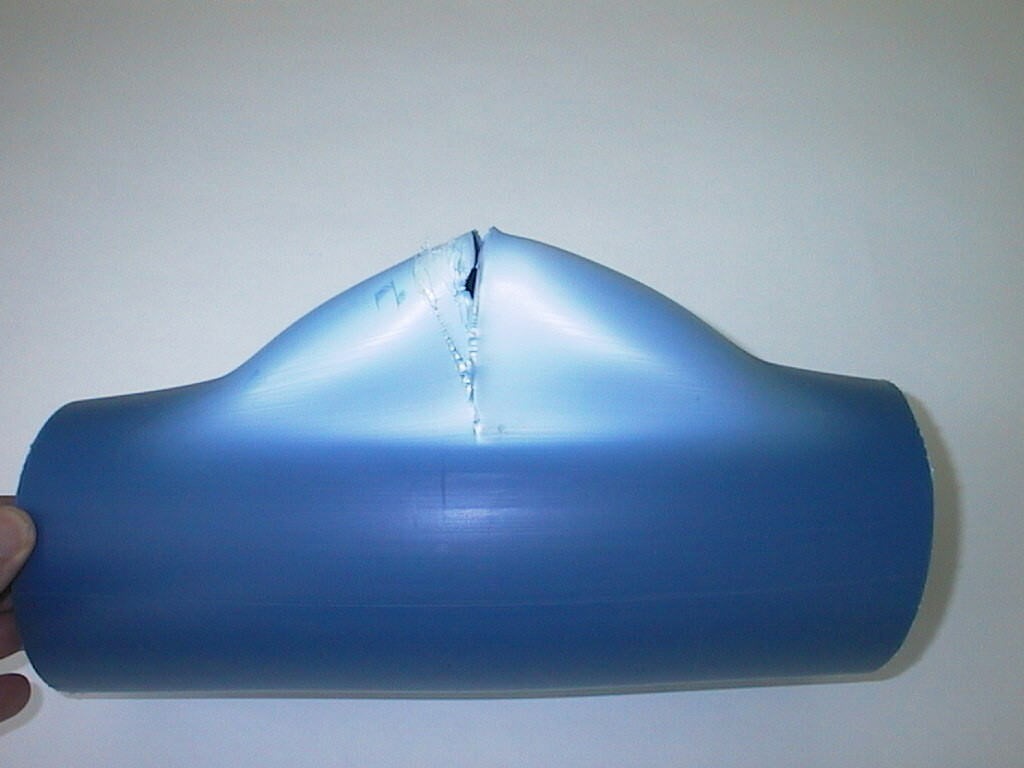
Polyvinyl chloride/chlorinated polyvinyl chloride (PVC/CPVC) pipes should not be used for compressed air. They fail in an unsafe, catastrophic manner. These materials can shatter and fragment during a failure, creating a hazardous situation from exploding PVC shrapnel.
Polypropylene (PP) pipes can be unsafe in cold conditions and shatter similarly to PVC. ABS pipes can be designed for compressed air, but their use may be limited due to specific compressor lubricant incompatibility issues. Fluoropolymer materials (for example, PVDF and ECTFE) are cost-prohibitive.
Polyethylene (HDPE) material can be engineered to handle compressed air applications because of its excellent physical and mechanical properties and broad chemical resistance. The material retains its ductile properties well below 0° F (~ -40° F). For example, if it were damaged by construction machinery or over-pressurized to failure, such failure would be in a safe manner. The pipe material would simply tear open, keeping the remaining pipe material intact, shown in the photo on the right.
However, PE resin for compressed air applications must be specially formulated and processed to handle the oxidative effect of air to enable long-term performance. Standard US domestic HDPE pipes, such as PE4710, are designed for fluids but not specifically for compressed air. For this reason, domestic polyethylene pipes must use both temperature and environmental design factors to adjust the pipe pressure ratings to an appropriately safe level. If lubricants are present, these factors could result in an 80% reduction in operating pressure at 100° F.
PE resin manufacturers in Europe formulate a resin class, known as PE100, to handle both liquid and air/gas applications. Asahi/America’s Air-Pro® piping system is manufactured from PE100 and designed specifically for compressed air applications. It has been used here in North America since 1992, with no known product failures. This PE100 piping system meets OSHA testing requirements and can be installed in compressed air applications both above and below ground. The manufacturing process of PE100 allows this pipe material to be applied at full pressure ratings, coincidental with built-in appropriate safety factors – typically a factor of 2.0.
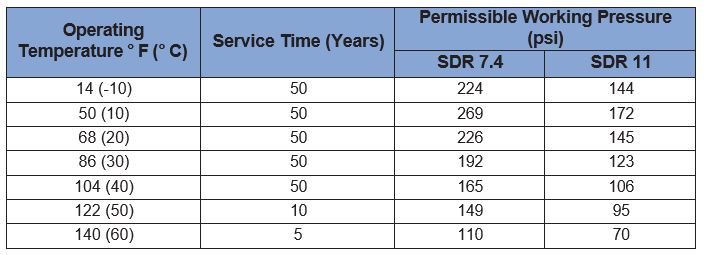
Because of its thermoplastic material makeup, PE100 pipe and fittings can be joined through a type of melt process, known as heat fusion. Heat fusion joining brings two melted surfaces together and allows them to cool under pressure, and produces one continuous piece, free of any foreign material or seams. The joint bonding area is as strong as the pipe itself. PE100 pipes and fittings are joined by either socket or butt fusion. With socket fusion, the pipe is inserted in socket fittings that have a slight taper; the tapered fitting increases the pressure on the pipe up to the stop. The entire insertion depth is the weld area. Butt fusion fittings have the same inside diameter (ID) and outside diameter (OD) for end-to-end fusing. Thus, two pipes can be butt fused without a coupling. Butt fusion always produces an external and internal bead that provides positive post-fusion joint inspection. The reliability and integrity of the PE butt fusion weld are why the natural gas industry has been using this fusion method for underground gas utility service for decades in the US.
There are myriad compressed air applications with different system requirements, including but not limited to, operating pressures and temperatures, chemical and environmental conditions, and permanence or mobility requirements. There is not a single piping system that can handle all requirements. However, Asahi/America’s Air-Pro® is a safe, reliable thermoplastic system to provide all the benefits for fluid process service in a compressed air system. For specifications, OSHA testing, and Air-Pro® case studies, please visit our website at www.www.asahi-america.com.
EDITOR’S NOTICE: Please note, the information in this article is for educational purposes only and does not supersede any Asahi/America technical information or product specifications. Please consult Asahi/America’s technical department at 1-800-343-3618 or pipe@asahi-america.com on all product applications in regards to material selection based on the pressure, temperature, environmental factors, chemical, media, application, and more.