

Inner Circle
Chemical Resistance With Confidence
Contributed by Dave Hurley, Product Information Manager
Confidence is essential when researching what material to use in an application. Beyond the function of valves, the material selection remains the most critical decision. Combining body material and elastomeric material compatibility to ensure a long service life is why customers continue to rely on Asahi/America for our recommendation.
Asahi/America bases chemical resistance rating on lab tests and real-world application testing. When we designate any material as incompatible, either it did not satisfy the application/performance testing in the lab, or a failure occurred while the product was in service. When field failures occur, we try to duplicate the customers’ experience in our R&D lab. There is often some uncertainty because the reported application may not be correct, but we cannot ignore the incident.
Our chemical compatibility is available on our website and is specific to our products. Asahi/America advises against using general guidance from other resources to select an Asahi/America product. In addition to the published information, we maintain volumes of unpublished testing to make customer-specific recommendations.
CPVC’s valve and piping resins have different chemical compatibility. Sodium or potassium hydroxide, commonly known as caustic solutions, have been proven to stress crack and fail when using Asahi/America CPVC valves. Additionally, we have found that FKM seals fail in caustic applications. Because of the slight risk of FKM failure, we recommend EPDM for these applications and have many customers with long-term success specifying EPDM in caustic solutions.
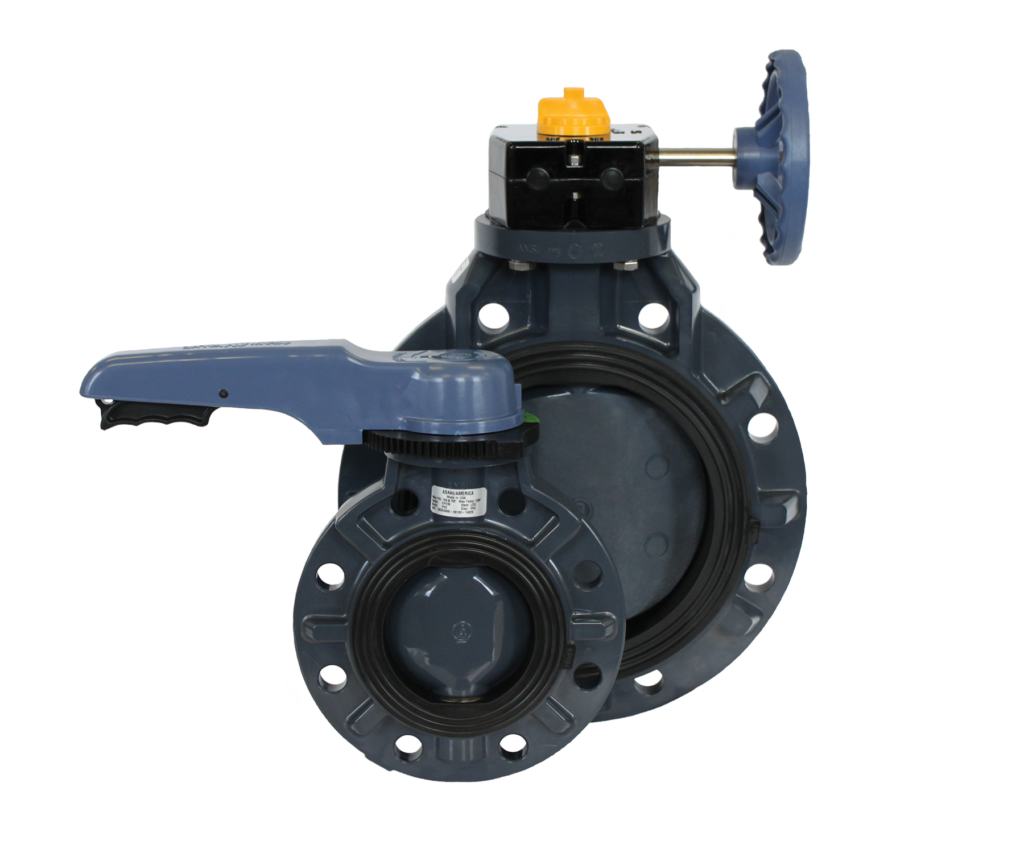
EPDM has proven, through application testing in swimming pools, to be moderately resistant to the effects of chlorinated water. In those situations, we recommend high-quality EPDM with a low amount of vulcanizing agents and fillers. The first point of attack will be the liner on a butterfly valve, but well-controlled water chemistry (i.e., chlorine that has fully dissolved in water) along with moderate temperature control will maintain an even concentration of chlorine in the water to lessen any effect. However, we do not recommend EPDM for chlorine gas or chlorine dioxide introduction, as EPDM has proven to be a solution in a closely controlled aqueous solution, like swimming pools.
Fluorinated elastomers like Asahi/America’s specialty FKM-F provide extreme resistance due to the strong fluorine bonds. When fitted with a PTFE diaphragm, we have moved to FKM-F for all true-union diaphragm valves. Our PTFE diaphragm is uniquely layered and not bonded construction, consisting of a wetted PTFE diaphragm, a PVDF gas barrier to prevent the gas from migrating out, and a protected EPDM cushion layer, with the compressor connection point molded into the PTFE. We call this a 3-layer sandwich, as they are all connected via the common molded compressor bayonet connector. Our diaphragms are also not laminated construction which tends to delaminate due to chemical penetration.
Is FKM-F just FFKM? Cost is the main difference between FFKM (Perfluoro-fluorine rubber) and FKM-F (Viflon® F rubber). FFKM is the most expensive specialty elastomer, chemically very similar in construction to PTFE. FKM-F provides similar chemical resistance properties as PTFE, but unlike FFKM, it has a lower production cost. Both contain fluorine, but FKM-F is blended to satisfy the requirements in plastic valve working temperature environments.
Sodium hypochlorite service is a widespread application we should look closely at. Our long-term recommendation is a PVC body, flanged diaphragm valve, with a 3-layer PTFE/PVDF/EPDM diaphragm. Asahi/America PVC material is chemically resistant to sodium hypochlorite, and the weak point is always the solvent-cemented joining.
Asahi/America flanged vinyl valves do not utilize solvent cement to connect a separate flange to the spigot. This exclusion eliminates cemented joints that come under attack from sodium hypochlorite. Our next and most popular solution is a Type-21 ball valve with molded flanged end connections; however, we also provide socket end valves, which tends to be preferred in the industry. O-rings are always made out of FKM in our ball valves for sodium hypochlorite applications. Asahi’s Chem Proline® Advanced PE piping system end connectors are also available with PVC body valves, so customers who choose the Advanced PE piping system to solve their sodium hypochlorite solutions can choose to weld on the valve instead of using flanges.
An additional feature we add is a 1/8″ vent hole for sodium hypochlorite and other off-gassing media (shown here). This inclusion eliminates pressurization in the cavity of the ball valve when the valve is closed. Extensive testing helped us to determine which side of the ball to “vent.” We found that when venting the ball on the upstream side of the valve, the fluid captured in the cavity of the ball when the valve is closed gets maintained by the positive upstream pressure, resulting in the cavity remaining fluidized—venting downstream causes the trapped product to crystalize as the upstream fluid does not maintain it.
EDITOR’S NOTICE: Please note, the information in this article is for educational purposes only and does not supersede any Asahi/America technical information or product specifications. Please consult Asahi/America’s technical department at 1-800-343-3618 or [email protected] on all product applications in regards to material selection based on the pressure, temperature, environmental factors, chemical, media, application, and more.