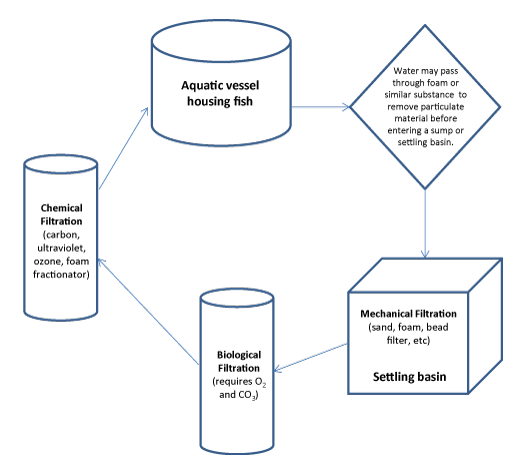
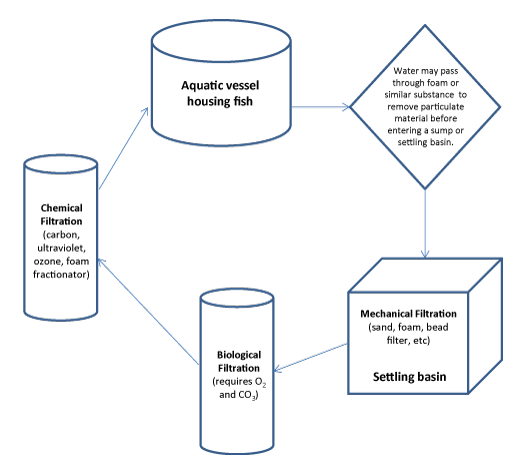
February 1, 2024
Inner Circle
How Different Thermoplastic Valves Operate in Aquatic Life Support Systems
Contributed by Zach Lehmann, Applications Engineer
The purpose of an aquatic life support system is to monitor and control the conditions of a body of water that is holding aquatic life. The six specific conditions of the water being controlled in these systems are quality, chemistry, biology, temperature, turnover, and clarity. Some of those conditions are more relevant than others, depending on the purpose of the vessel holding the aquatic life. In an aquarium setting, the purpose is to display the life in the tank; thus, clarity is more important than in a fish farm, where the visibility of the fish is less crucial. All aquatic life support systems can be categorized into one of three general styles: open systems, semi-open systems, and closed systems. Each of these three systems has varying degrees of required components and design complexity depending on the purpose and scale of the water body being maintained.
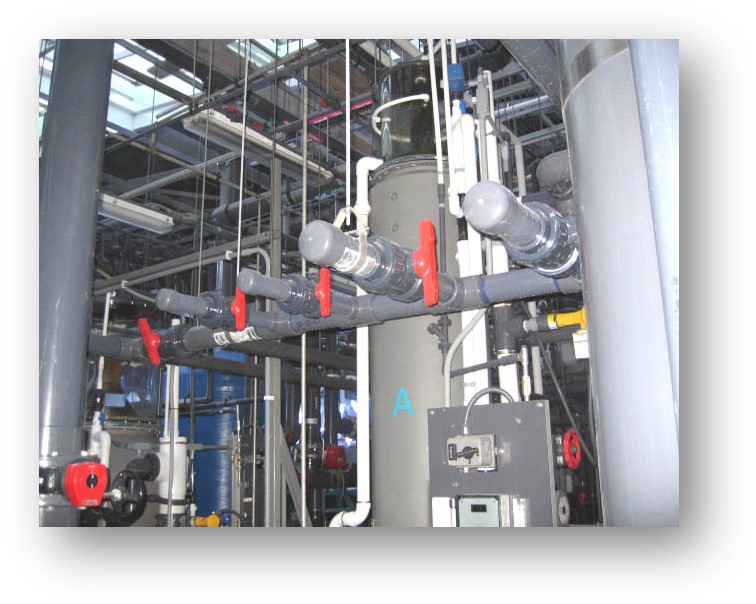
Open aquatic life support systems have some body of source water that runs through a culture facility before being discharged without any form of recirculation. Semi-open aquatic life support systems use a body of source water but can also recirculate treated water back through the system to further control water quality or reduce reliance on the body of source water. Closed aquatic life support systems have no external body of source water and are entirely reliant on recirculating water within the system. There are examples of all three aquatic life support systems that can occur naturally as well as artificially. The most common man-made examples of these systems are aquariums, fish farms, raceways, hatcheries, and zoo exhibits with water features.
There are five main subsections that can constitute an aquatic life support system that has a recirculation component to it: the main tank or area where the aquatic life is held, the settling basin that holds water just before and/or after the water has been treated, a mechanical filtration system, a chemical filtration system, and a biological filtration system. Biological filters provide a substrate and house nitrifying bacteria that help neutralize ammonia and other nitrogenous waste in the water, mainly produced by the aquatic life in the tank. Mechanical filters utilize porous physical materials like beds of sand or beads to filter out larger waste materials, such as uneaten food or debris, before the water is taken to other quality treating sections. Chemical filtration utilizes various chemicals to remove toxins and colored compounds to improve water quality and clarity.
These different sections of aquatic life support systems depend on valves to control the flow, pressure, and distribution of media throughout each process. Since most systems that hold aquatic life are under lower pressures and temperatures, thermoplastics are the ideal material to use to make valves based on price point, required supports, and ease of operation. Of all the available valve material options, the most commonly used in these systems are PVC/EPDM because they are best rated for use with low levels of chlorine and O-zone, the most common agents used in chemical filtration systems. Saltwater also holds up well in PVC/EPDM. While the material in most of the valves remains the same, there are a few different types of valves that could be used in different parts of the system based on the strengths and weaknesses of the valve. Knowing how to choose the right valve for the right application is essential.
How to choose the right valve for a life support system
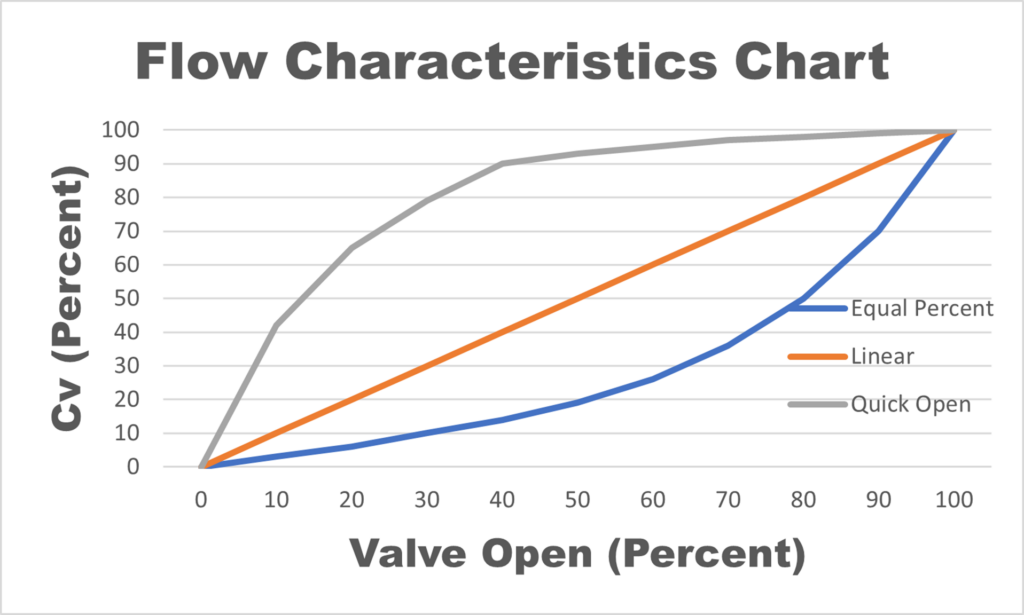
There are four main styles of valves used in aquatic life support systems. Ball valves, butterfly valves, gate/plug valves, and precision control valves. Each valve type can be categorized by the flow characteristics it exhibits during its full stroke. The three most common styles of flow characteristics are linear, equal percent, and quick open. These are determined based on each valve’s calculated flow coefficient (Cv), which can be used to determine the effect each valve will have on the head loss of the system—the value of the flow coefficient changes depending on how open the valve is. In valves with linear flows, the Cv value changes proportionally as the percentage of the valve opening changes. This proportional change means small movements in valve stroke travel will similarly have small changes in the flow rate or pressure drop in the system. Linear valves are great for achieving accurate flow control applications in systems. Equal percent valves produce an equal percentage of change in existing flow from equal increments of valve travel. This relationship means that when the valve is nearly closed, the flow is low, and there is little change in flow when moved a short distance, but when the valve is nearly fully open, there are large changes in flow when moved a short distance. Equal percent valves are mainly used for pressure control in the system. Quick opening valves jump to near maximum Cv with just a small amount of travel from fully closed. Quick opening valves have poor flow control capabilities and are mainly used as shutoff valves that are either fully open or fully closed.
Full bore ball valves are quarter-turn valves with a smaller range in available sizes when made out of thermoplastics since large-scale ball valves can be difficult to operate manually and cost more to produce. Ball valves are also more prone to being damaged by suspended particles in the line and are typically located after some form of mechanical filter or on feed lines into the system that don’t have any presence of particulate. Ball valves have quick opening flow characteristics and are typically used as shutoff valves with a low pressure drop. Some ball valves have different shapes cut into the ball, making the fully open valve no longer full bore, producing a more linear flow characteristic to be used as a cost-effective control valve in applications where flow variability or a larger pressure drop is required.
Butterfly valves are quarter-turn valves with the most extensive range of sizes that can handle most types of particulates in the line. They struggle with longer particulates or particulates that can agglutinate since the valve is not full bore, which can damage the liner or make the valve difficult to fully seat. This typically means butterfly valves are useful in almost all filtration systems but not great as a drain off of a main tank or aquatic life holding vessel. With an equal percent flow characteristic, butterfly valves can be utilized as either a shutoff valve or a moderate flow control valve, adding to their versatility. They also have a moderately low pressure drop.
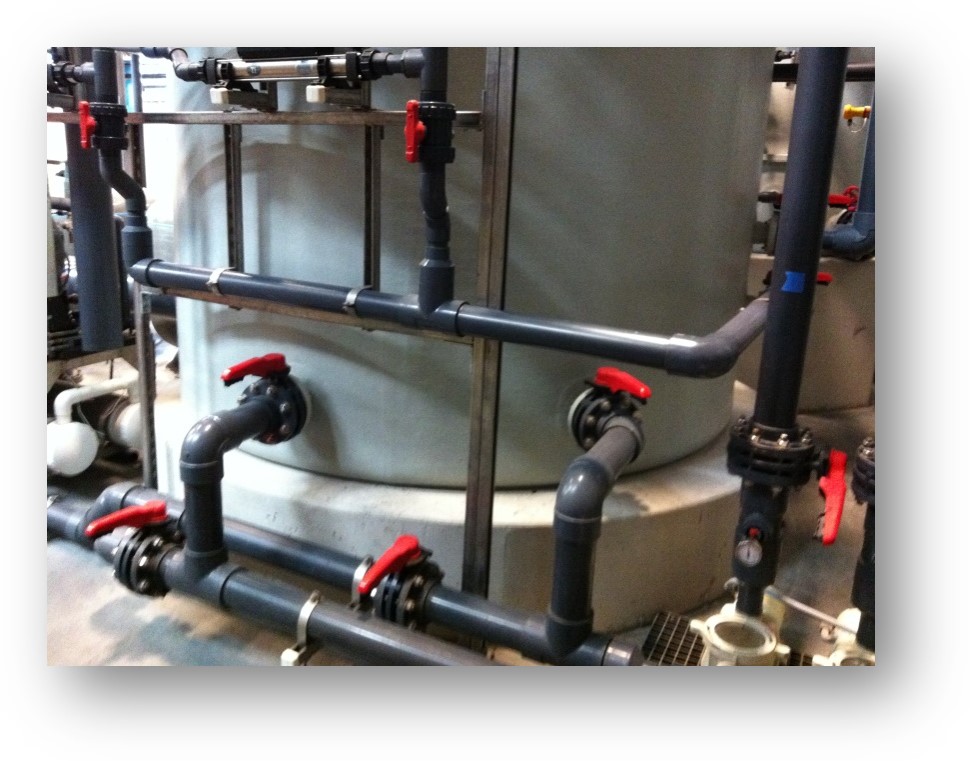
Plug or gate valves are multiturn valves that come in a moderate range of sizes and are full bore when fully opened, giving them a low pressure drop. They have a quick opening flow and are used exclusively as a shutoff valve since partially opening the valve can lead to chatter from the plug obstructing flow, which can damage the plug or lead to harmful vibrations to the surrounding plumbing. Plug/gate valves are good with suspended particles and have drainable cavities, allowing them to be cleaned or serviced without removing them from the line. This ability to handle most particulates and the lack of need for an isolation valve to service make them the main valve used as an outlet or drain on the aquatic life tank.
Precision control valves can come in various styles, but the main thermoplastic valves used for the highest level of flow control are diaphragm valves and globe valves. These valves are not full bore and have high pressure drops. Flow characteristics can vary depending on the style and trim of these valves, but are typically equal percent, linear, or some hybrid of the two. These valves are always multiturn, allowing for the most minor adjustments in travel of the diagram or globe plug to have the finest adjustments in flow. Since these valves are at a higher price point, they are only utilized when the most precise flow adjustments are required, like in specific dosing applications of filtration systems.
Aquatic life support systems are imperative to all zoos, aquariums, fish farms, and all other vessels created to house aquatic life, and valves drive all the processes required to maintain the stable living conditions of those important industries. No matter the size of the operation, from the largest closed-system aquariums in the world to the simplest open-system fish farms, Asahi/America has been supplying the best industrial-grade thermoplastic valves needed to keep these facilities running for years.
EDITOR’S NOTICE: Please note, the information in this article is for educational purposes only and does not supersede any Asahi/America technical information or product specifications. Please consult Asahi/America’s technical department at 1-800-343-3618 or [email protected] on all product applications in regards to material selection based on the pressure, temperature, environmental factors, chemical, media, application, and more.