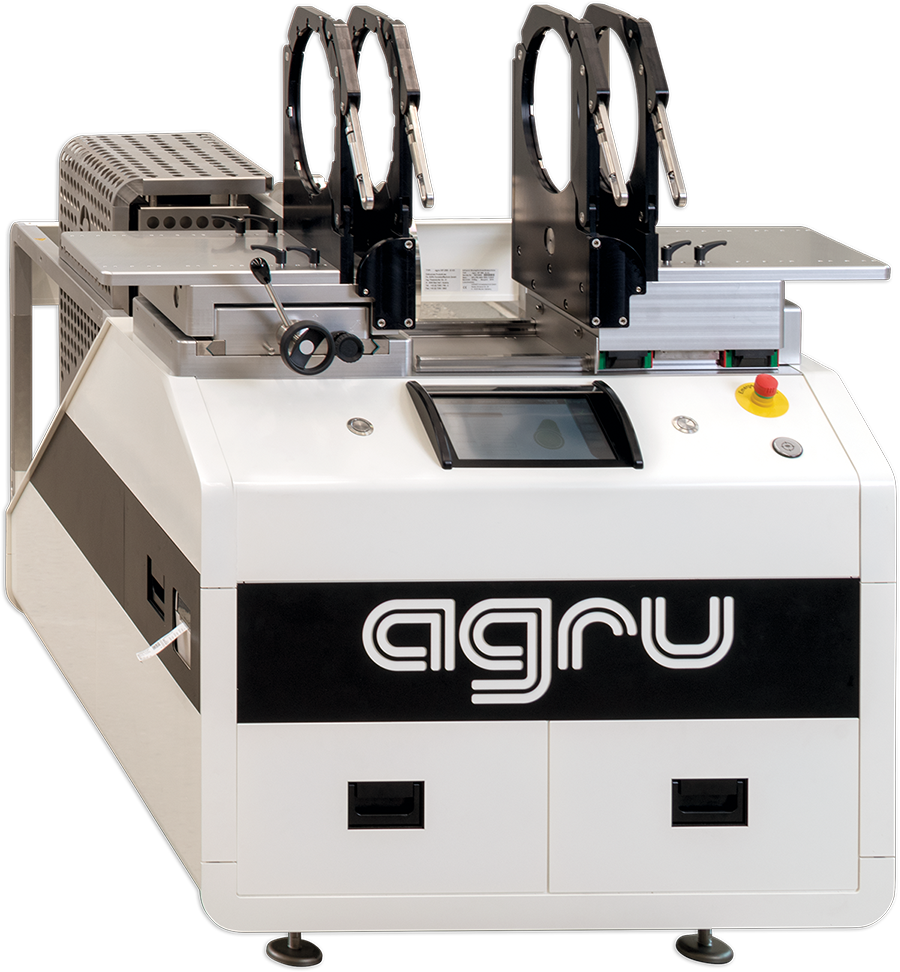
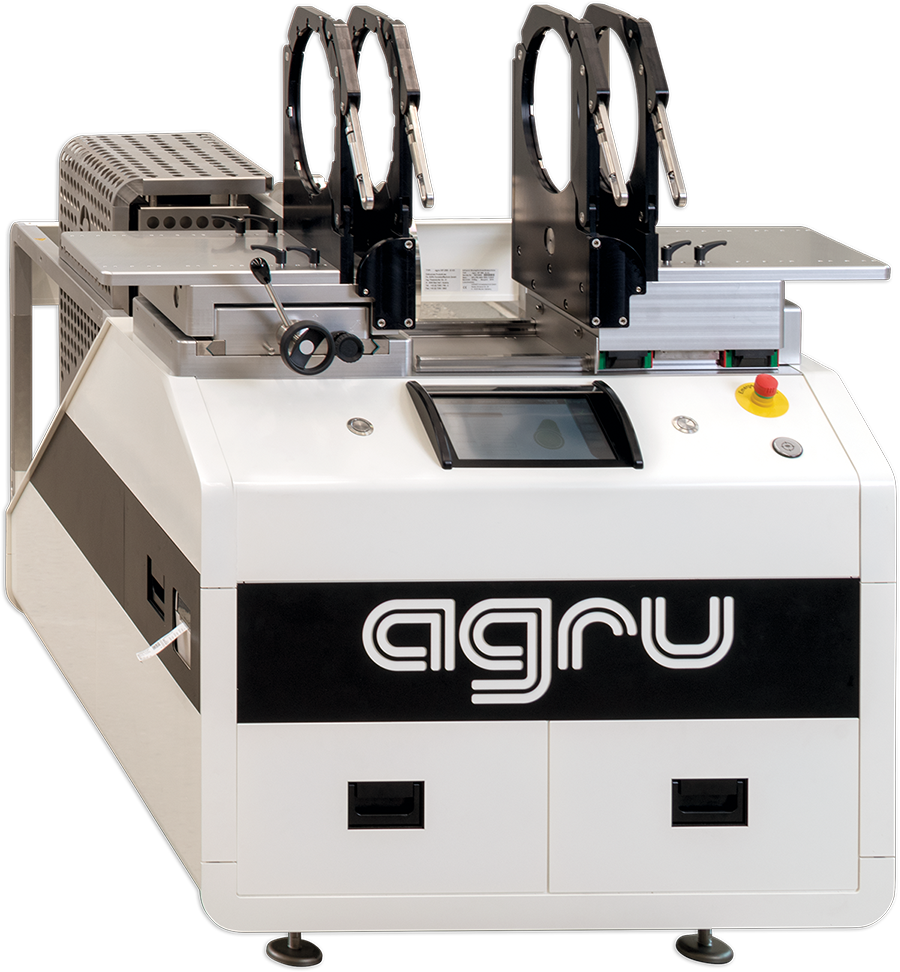
mai 1, 2021
Cercle intérieur
Systèmes de tuyauterie de haute pureté : Sélection des matériaux et soudage
Contribution de Dave Stiles, responsable du développement commercial, Produits de haute pureté
Dans la fabrication des semi-conducteurs et dans l’industrie des sciences de la vie, l’eau purifiée (PW), l’eau déionisée (DI) et l’eau ultrapurifiée (UPW) jouent un rôle essentiel dans la qualité du produit final. La spécification des matériaux de tuyauterie et des méthodes d’assemblage appropriés est une considération importante pour les ingénieurs en systèmes MEP. Les ingénieurs spécificateurs de ces disciplines ont déjà une bonne connaissance de la sélection des matériaux, mais saviez-vous que les méthodes d’assemblage peuvent avoir un impact plus important sur les performances du système ? Le prescripteur doit trouver un équilibre entre la fiabilité, la performance, la conformité réglementaire et l’économie. Examinons les méthodes d’assemblage, les applications typiques et les limites de ces méthodes.
En règle générale, le processus de conception commence par un examen des exigences de l’utilisateur final en matière de qualité de l’eau. La liste des normes établies est longue. Chacune d’entre elles a été développée pour répondre à une application donnée. Certaines mettent l’accent sur la résistivité, tandis que d’autres donnent la priorité au carbone organique total (COT), aux particules ou aux charges bactériennes. Heureusement, ces normes peuvent être réparties en trois grands groupes qui s’alignent sur les systèmes de tuyaux de haute pureté d’Asahi/America (voir tableau 1). Bien qu’il existe un certain degré de flexibilité, le prescripteur doit veiller à prendre en compte les vannes disponibles, les tailles de tuyaux et les plages de pression qui peuvent limiter la sélection.
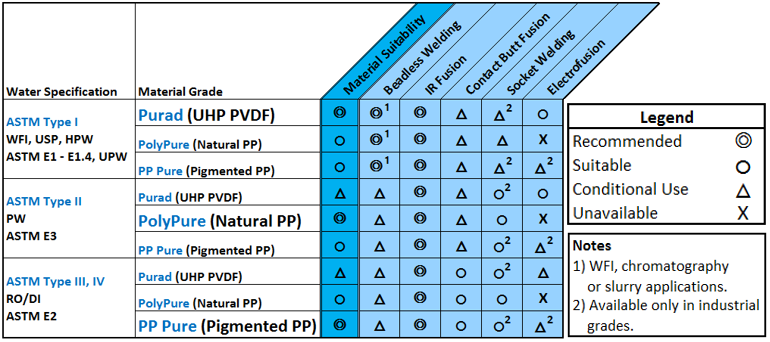
Après avoir défini une qualité de matériau appropriée, il faut se pencher sur la question des méthodes de soudage. Des soudures ou des joints mécaniques inappropriés peuvent gravement dégrader un système. La fusion infrarouge (IR) se distingue par ses excellentes performances en raison de la petite taille de ses cordons et de sa répétabilité. Cela s’explique par l’utilisation d’une technologie de contrôle de la force qui fait appel à un capteur de pression, à un entraînement par vis sans fin et à des paramètres préprogrammés. Le capteur de pression limite la force d’assemblage et empêche qu’une trop grande quantité de matériau fondu ne soit chassée de la zone affectée par la chaleur, ce qui provoquerait une soudure froide. Cette méthode s’oppose à la technologie de contrôle de la distance que l’on trouve dans de nombreux outils plus anciens. En outre, la méthode de chauffage sans contact n’introduit pas de contaminants dans le cordon. Dans la plupart des applications de haute pureté, la fusion IR s’avère être une solution optimale. Cependant, toute règle comporte des exceptions.
Notamment, le soudage sans cordon, qui utilise un ballon spécialement conçu à l’intérieur de la tuyauterie pendant le processus de soudage pour éliminer tout cordon, peut être préféré pour les systèmes qui doivent être entièrement vidangeables ou qui sont particulièrement sensibles à la croissance de biofilms, tels que l’eau pour injection (WFI) ou la chromatographie. Si vous optez pour la méthode sans cordon, sachez qu’il s’agit de la méthode de soudage la plus lente et qu’elle est relativement coûteuse. L’installateur refond le thermoplastique et forme un matériau homogène. Avec un équipement de soudage automatisé, le soudage sans cordon est assez fiable, mais il peut être décourageant pour les entrepreneurs qui ne sont pas familiarisés avec le processus. Le soudage sans cordon demande de la planification car le ballon interne doit être retiré après la soudure. Ce point est abordé dans les procédures de formation d’Asahi/America avant le démarrage du chantier. Comme pour toutes les méthodes de soudage, il est essentiel que les fabricants reçoivent une formation conforme aux normes et aux codes en vigueur avant d’effectuer tout travail sur un projet. Le programme de certification d’Asahi consiste généralement à former les opérateurs à l’utilisation de l’équipement et à s’assurer qu’ils sont capables de produire des soudures fiables.
Le soudage par emboîtement est une méthode d’assemblage très simple qui utilise une douille chauffante et un raccord qui fusionnent le tuyau. Cette méthode est intéressante pour les applications moins critiques ou les petits travaux pour lesquels le coût d’utilisation d’un outil de soudage à infrarouge est prohibitif. Le soudage par emboîtement donne lieu à de grandes perles internes et à des crevasses qui peuvent favoriser la croissance du biofilm. Si l’application n’est pas bio/pharmaceutique et ne nécessite pas un drainage complet, envisagez d’autoriser le soudage par emboîtement pour un certain pourcentage de soudures. Cette flexibilité permet aux entrepreneurs d’utiliser cette méthode en même temps que la fusion IR pour les endroits difficiles tels que les raccordements finaux ou les joints impossibles à réaliser autrement.
La fusion bout à bout par contact est une autre option viable pour certaines applications. Le cordon interne est plus large que celui du soudage IR, mais plus petit que celui du soudage par emboîtement. Le procédé est moins sensible à la circulation de l’air que le soudage IR et peut donc être utilisé dans une grande variété d’environnements de fabrication. Malheureusement, il peut également introduire un certain niveau de contamination dans le cordon. Cette méthode de soudage est la plus courante pour les applications chimiques, le double confinement ou l’utilisation industrielle.
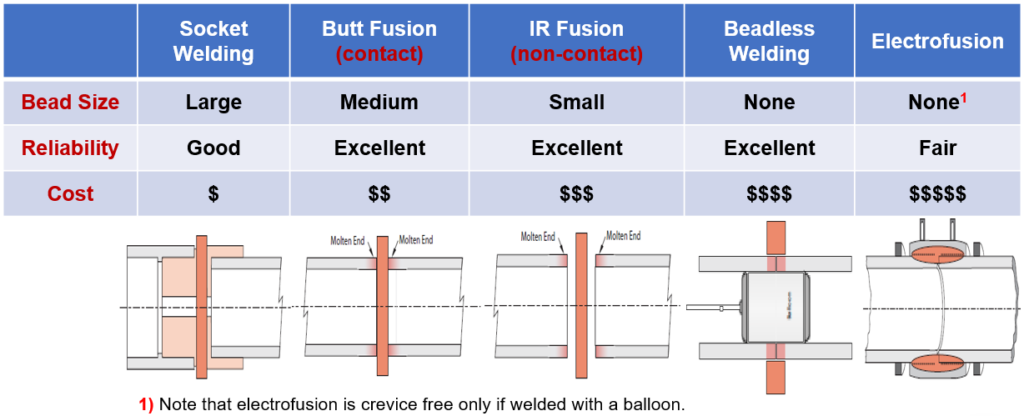
L’électrofusion est une méthode d’assemblage qui utilise la chaleur produite par la résistance d’une bobine électrique lorsqu’elle est alimentée. La bobine des matériaux d’Asahi/America est toujours intégrée dans le raccord afin d’éviter toute exposition au fluide du système. Cette technique n’a qu’un rôle limité dans les systèmes de haute pureté et n’est généralement recommandée que lorsqu’aucune autre option n’est disponible. Elle est excellente pour les raccordements difficiles à atteindre, mais elle laisse une petite crevasse entre les extrémités des tuyaux. Cette crevasse peut abriter un biofilm et doit donc être évitée dans les applications qui exigent un faible COT. Les raccords pour les systèmes en polypropylène sont techniquement de qualité industrielle. Leur disponibilité n’est mentionnée qu’à titre d’information et ne constitue pas une recommandation d’utilisation dans des applications de haute pureté. Cependant, dans le cas du PVDF d’un demi-pouce à deux pouces, Asahi/America propose un système unique qui utilise un ballon inséré dans le diamètre intérieur du tuyau. Le ballon de haute pureté est gonflé pendant la fusion, ce qui exerce une pression sur la paroi interne et empêche la formation d’une crevasse.
La plupart des entrepreneurs possèdent leur propre équipement de soudage et emploient des personnes qui ont reçu des certifications spéciales de l’American Welding Society (AWS) pour effectuer le soudage des thermoplastiques. Pour ceux qui ne possèdent pas leur propre équipement de soudage, Asahi/America dispose d’un parc d’équipements de fusion. Il est important de spécifier qui peut souder les tuyauteries pour les applications. Le processus de certification d’Asahi garantit que les fabricants reçoivent une formation suffisante pour utiliser l’équipement et effectuer des soudures de manière fiable. Pour plus d’informations, Asahi/America peut fournir un guide complet de conception technique et des spécifications de produits, ainsi que des opportunités de déjeuner et de formation pour votre équipe. N’hésitez pas à contacter l’équipe Asahi BDM pour toute question.
AVIS DE L’ÉDITEUR : Veuillez noter que les informations contenues dans cet article sont uniquement destinées à des fins éducatives et ne remplacent pas les informations techniques ou les spécifications des produits d’Asahi/America.
Veuillez consulter le service technique d’Asahi/America au 1-800-343-3618 ou à l’adresse pipe@asahi-america.com pour toutes les applications de produits en ce qui concerne la sélection des matériaux en fonction de la pression, de la température, des facteurs environnementaux, des produits chimiques, des médias, de l’application, etc.