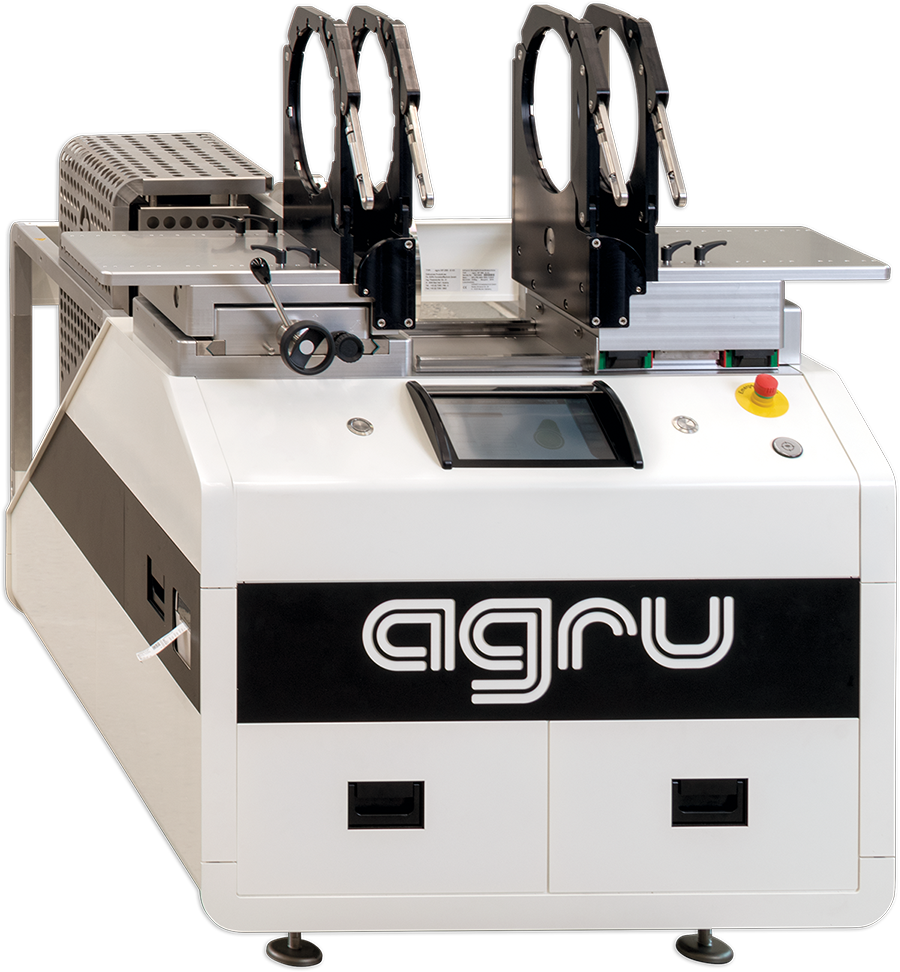
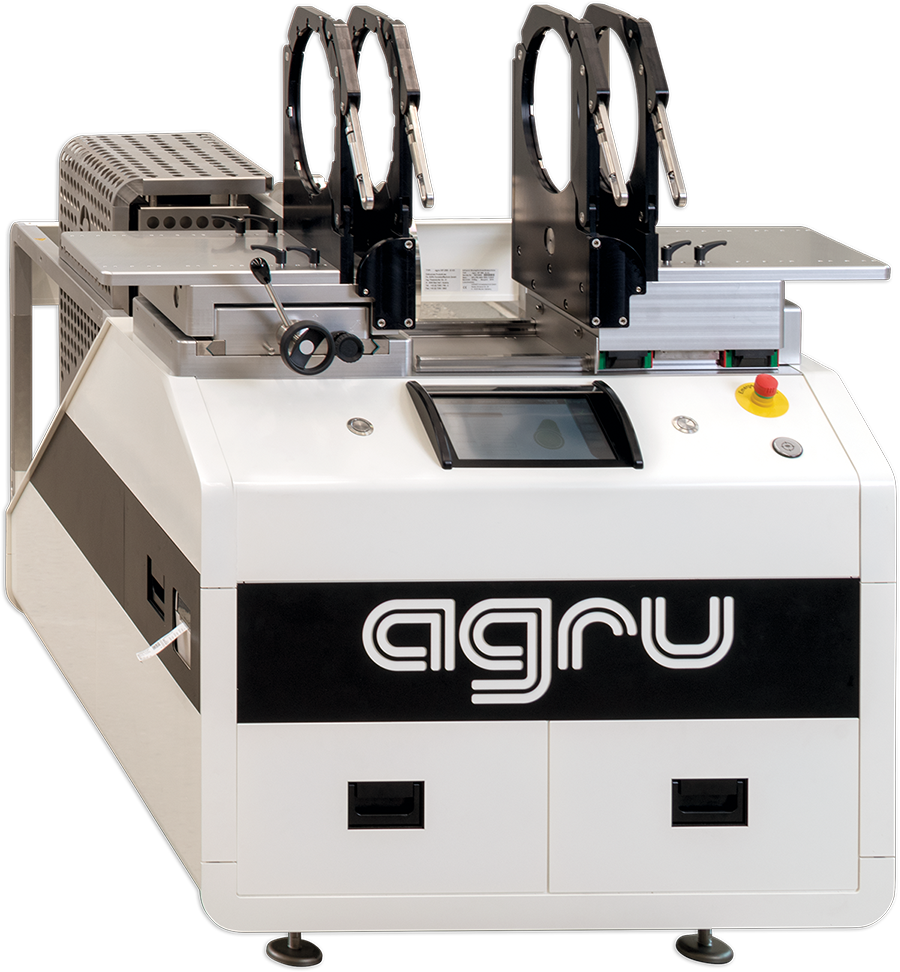
mayo 1, 2021
Círculo interno
Sistemas de tuberías de alta pureza: Selección de materiales y soldadura
Contribución de Dave Stiles, Director de Desarrollo Comercial, Productos de Alta Pureza
Tanto en la fabricación de semiconductores como en la industria de las ciencias de la vida, el agua purificada (PW), el agua desionizada (DI) y el agua ultrapurificada (UPW) desempeñan papeles críticos en la calidad del producto final. La especificación de materiales de tuberías y métodos de unión adecuados es una consideración importante para los ingenieros de sistemas MEP. Los ingenieros encargados de las especificaciones en estas disciplinas ya conocen bien la selección de materiales, pero ¿sabías que los métodos de unión pueden tener un mayor impacto en el rendimiento del sistema? Un especificador debe encontrar un equilibrio entre fiabilidad, rendimiento, cumplimiento de la normativa y economía. Echemos un vistazo a los métodos de unión, las aplicaciones típicas y las limitaciones de esos métodos.
Normalmente, el proceso de diseño comienza con una revisión de los requisitos de calidad del agua de los usuarios finales. La lista de normas establecidas es amplia. Cada una se ha desarrollado para adaptarse a una aplicación determinada. Algunas ponen el mayor énfasis en la resistividad, mientras que otras dan prioridad al carbono orgánico total (COT), las partículas o las cargas bacterianas. Afortunadamente, estas normas pueden desglosarse en tres grandes grupos que se ajustan a los sistemas de tuberías de alta pureza de Asahi/America (véase la tabla 1). Aunque existe cierto grado de flexibilidad, el especificador debe tener en cuenta las válvulas disponibles, los tamaños de tubería y los rangos de presión que pueden limitar la selección.
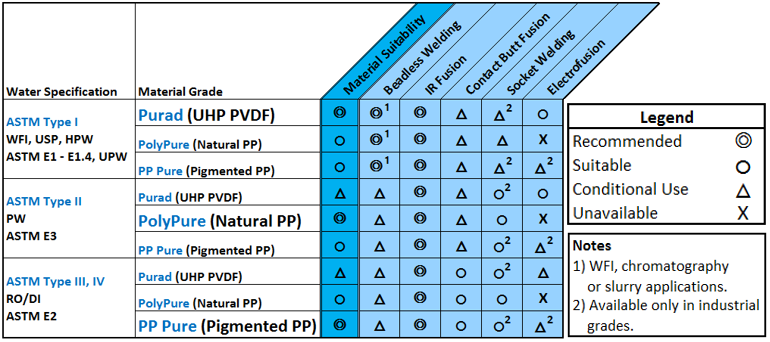
Tras definir un grado de material adecuado, hay que abordar la cuestión de los métodos de soldadura. Unas soldaduras o uniones mecánicas inadecuadas pueden degradar gravemente un sistema. La fusión por infrarrojos (IR) destaca por su excelente rendimiento debido al pequeño tamaño de su cordón y a su repetibilidad. Esto se debe al uso de una tecnología de control de fuerza que emplea un transductor de presión, un tornillo sin fin y parámetros preprogramados. El transductor de presión limita la fuerza de unión y evita que salga demasiado material fundido de la zona afectada por el calor, provocando una soldadura en frío. Este método contrasta con la tecnología de control de distancia de muchas herramientas antiguas. Además, el método de calentamiento sin contacto no introduce contaminantes en el cordón. En la mayoría de las aplicaciones de alta pureza, la fusión por IR resulta ser una solución óptima. Sin embargo, toda regla tiene sus excepciones.
En particular, la soldadura sin cordón, que utiliza un globo especialmente diseñado dentro de la tubería durante el proceso de soldadura para eliminar cualquier cordón, puede ser preferible para sistemas que necesitan ser totalmente drenables o son especialmente sensibles al crecimiento de biopelículas, como el agua para inyección (WFI) o la cromatografía. Cuando se opta por la soldadura sin cordón, hay que tener en cuenta que es el método de soldadura más lento y relativamente caro. El instalador vuelve a fundir el termoplástico y forma un material homogéneo. Con equipos de soldadura automatizados, la soldadura sin cordón es bastante fiable, pero puede resultar desalentadora para los contratistas que no estén familiarizados con el proceso. La soldadura sin cordón requiere planificación porque el globo interno debe retirarse después de la soldadura. Esto se trata en los procedimientos de formación de Asahi/America antes de iniciar el trabajo. Como ocurre con todos los métodos de soldadura, es fundamental que los fabricantes reciban una formación que cumpla todas las normas y códigos vigentes antes de realizar cualquier trabajo en un proyecto. El programa de certificación de Asahi suele consistir en formar a los operarios en el uso del equipo y asegurarse de que son capaces de producir soldaduras fiables.
La soldadura por encastre es un método muy sencillo de unión que utiliza un casquillo calefactor y un acoplamiento, que fusiona el tubo. Este método resulta útil en aplicaciones menos críticas o en trabajos pequeños en los que el coste de utilizar una herramienta de soldadura por infrarrojos es prohibitivo. La soldadura por encastre da lugar a grandes cordones internos y hendiduras que pueden favorecer el crecimiento de biopelículas. Si la aplicación no es bio/farmacéutica y requiere un drenaje completo, considera la posibilidad de permitir la soldadura por encastre para un determinado porcentaje de soldaduras. Esta flexibilidad ofrece a los contratistas la posibilidad de utilizar este método junto con la fusión por infrarrojos para lugares difíciles, como las uniones finales o uniones imposibles por otros motivos.
La fusión a tope por contacto es otra opción viable para algunas aplicaciones. El cordón interno es mayor que el de la soldadura por IR, pero menor que el de la soldadura por encastre. El proceso es menos sensible a la circulación de aire que la soldadura por IR y, por tanto, puede realizarse en una amplia variedad de entornos de fabricación. Por desgracia, también puede introducir cierto nivel de contaminación en el cordón. Este método de soldadura es el más habitual para aplicaciones químicas, de doble contención o de uso industrial.
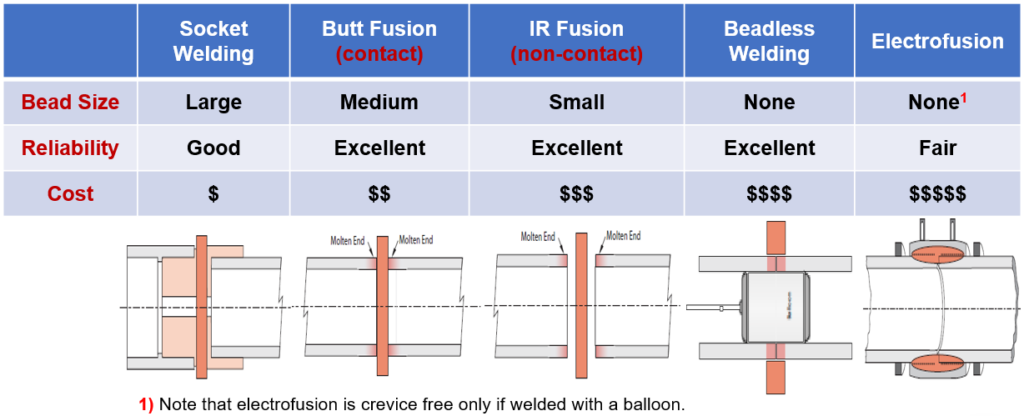
La electrofusión es un método de unión que utiliza el calor obtenido de la resistencia de una bobina eléctrica cuando se aplica energía. La bobina de los materiales de Asahi/America siempre está incrustada dentro del acoplamiento para evitar la exposición al fluido del sistema. Esta técnica sólo tiene un papel limitado en los sistemas de alta pureza y, en general, sólo se recomienda cuando no hay otra opción disponible. Es excelente para empalmes de difícil acceso, pero dejará una pequeña hendidura entre los extremos de las tuberías. Esta hendidura puede albergar biopelículas, por lo que debe evitarse en aplicaciones que exijan un COT bajo. Los acoplamientos para sistemas de polipropileno son técnicamente de calidad industrial. Su disponibilidad se menciona sólo con fines informativos y no como recomendación de que se utilicen en aplicaciones de alta pureza. Sin embargo, en el caso del PVDF de media pulgada a dos pulgadas, Asahi/America ofrece un sistema exclusivo que utiliza un globo insertado en el diámetro interior de la tubería. El globo de alta pureza se infla durante la fusión, lo que presiona contra la pared interior impidiendo la formación de una hendidura.
La mayoría de los contratistas poseen equipos de soldadura y emplean a personas que han recibido certificaciones especiales de la Sociedad Americana de Soldadura (AWS) para realizar soldaduras termoplásticas. Para los que no tienen equipo de soldadura propio, Asahi/America mantiene una flota de equipos de fusión. Es importante especificar quién puede soldar tuberías para las aplicaciones. El proceso de certificación de Asahi garantiza que los fabricantes reciban formación suficiente para manejar el equipo y realizar soldaduras fiables. Si deseas más información, Asahi/America puede proporcionarte una completa guía de diseño de ingeniería y especificaciones de productos, así como oportunidades de almuerzo y aprendizaje para tu equipo. No dudes en ponerte en contacto con el equipo de BDM de Asahi si tienes alguna pregunta.
AVISO DEL EDITOR: Ten en cuenta que la información de este artículo sólo tiene fines educativos y no sustituye a ninguna información técnica ni especificación de producto de Asahi/America.
Consulta al departamento técnico de Asahi/America en el 1-800-343-3618 o en pipe@asahi-america.com sobre todas las aplicaciones de productos en lo que respecta a la selección de materiales en función de la presión, la temperatura, los factores medioambientales, los productos químicos, los medios, la aplicación, etc.